4A 5A TB6600 Single Axis Stepper Motor Driver Controller Board CNC Engraving Machine 1 Axis Stepping Motor Driver Module
4A 5A TB6600 Single Axis Stepper Motor Driver Controller Board CNC Engraving Machine 1 Axis Stepping Motor Driver Module
SKU:010700- guaranteeQuality checked
- Special gift cardsSpecial gift cards
- Free return Within 60 days
- Consultancy86-0755-85201155
4A-TB6600
Specifications:
Supply Voltage: 9~42VDC
Max Drive Current: 4A
Chopping Frequency: 20KHZ
Features:
Bipolar constant current chopper
High-speed optocoupler signal isolation input
Electrical input signal is TTL compatible
Stationary current is automatically reduced by half
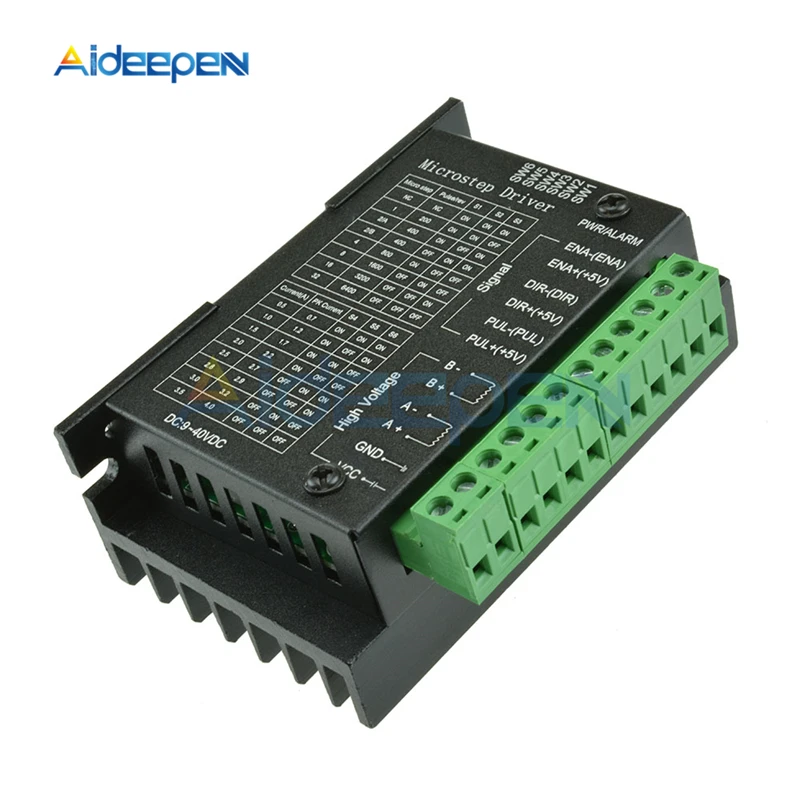
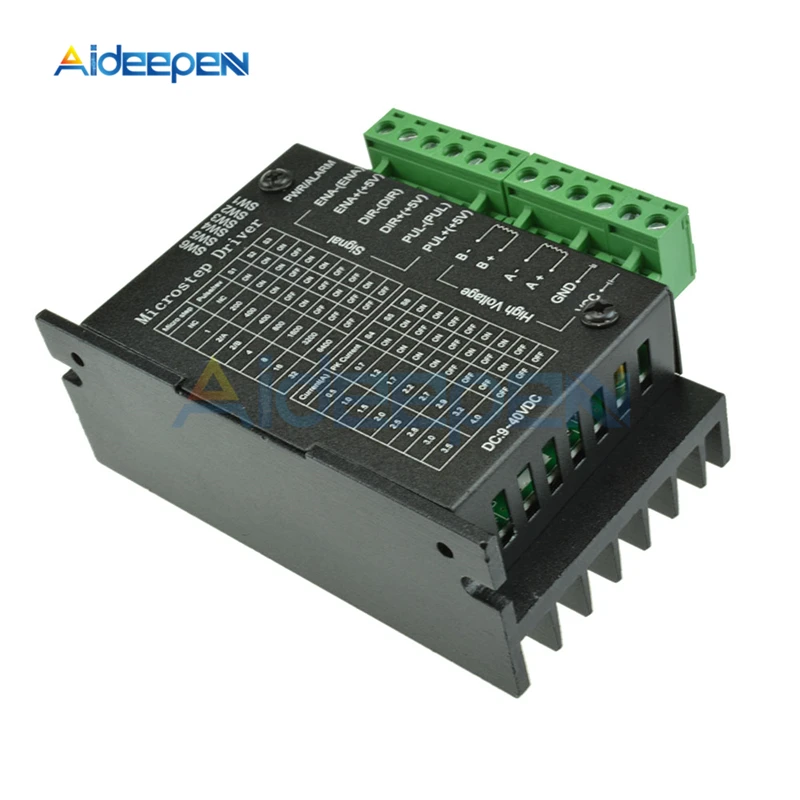

5A-TB6600
HY-DIV268N-5A subdivision-type two-phase hybrid stepping motor drive using DC 12 ~ 48V power supply, suitable for drive
Two-phase hybrid stepping motor dynamic voltage 12 to 48V, the current is less than 5A outer diameter of 35 to 86 mm. This drive using the drive's current loop subdivision control, the motor torque ripple is very small, low-speed running is very smooth, almost no vibration and noise. High-speed torque is much higher than other two-phase drive, high positioning accuracy. Widely used in the engraving machine, CNC machine tools, packaging machinery and other high resolution requirements on the device.
The main features
- average current control, two-phase sinusoidal current drive output
- DC 12 ~ 48V power supply, the internal integration of 12V and 5V regulator
- optically isolated signal input / output
- overvoltage, undervoltage, overcurrent, and white short-circuit protection
- Input voltage DC 12 ~ 48V input
- The input current of 1 to 5 amps, select the drive a stepper motor.
- Output current of 0.2A ~ 5A
- Temperature Operating Temperature -10 to 45 ℃; Storage temperature -40 ℃ to 70 ℃
- Humidity not condensing, not drops
- Gas prohibit combustible gas and conductive dust
- Weight 200 grams
Control signal interface
- Figure 1 is a wiring schematic of the drive
- 1, the definition of control signals
PUL +: step pulse signal is input side or the positive pulse signal input positive terminal
PUL-: the negative input of the negative input pulse signal or a positive pulse signal
DIR +: stepping direction signal input to the positive terminal or negative pulse signal input to the positive terminal
DIR -: stepping direction signal input of the negative side or reverse step pulse signal input negative terminal
EN +: offline can reset signal input side is
EN-: offline can reset signal input negative terminal
Offline enable signal is active, reset drive failure to prohibit any pulse, the output of the drive
Power component is turned off, the motor holding torque.
- Control signal connections
- PC control signal can be high, also can be low effective. When active high, the control signal
- The negative side together as a signal to active low, positive side of all control signals together as a signal common.
- For example, open-collector and PNP output interface circuit diagram is as follows:
Figure 2. Input interface circuit (common cathode connection)
- Note: the VCC is 5V, R short;
- VCC value of 12V, R 1K, more than 1/8W resistor;
- VCC value of 24V, R 2K, more than 1/8W resistor;
Function selection (DIP switch on the drive panel)
- Set the motor per revolution steps
The drive to set the number of steps per motor revolution is 200 (whole step), 400 (2 segments), 1600 (8 segments), 3200 steps (16 segments).
The user can drive the front panel DIP switch SW3 is SW4 bit of the drive to set the number of steps (such as Table 1):
Table 1
- Set the output phase current
- To drive torque stepper motor, the user can drive panel DIP switch
- SW1, SW2 is to set the drive output phase current (RMS) unit amperes, the switch position
- Corresponding to the output current, output current value corresponding different types of drive. Concrete are shown in Table 2.
- Output Current (A
Table 2
Current setting
- the semi-flow functionality
- The semi-flow function is a step pulse 200ms, the driver output current is automatically reduced to the rated output current50%, used to prevent motor heating.
Fourth, the power interface
- 1, DC +, DC-: to connect the drive power
- DC +: DC power level, power supply voltage DC 12 to 48V. The maximum current is 5A. The
DC-: DC power supply negative level.
2, A + A-B + B-: to connect the two-phase hybrid stepping motor
Drive and two-phase hybrid stepper motor's connection with the four-wire system, the motor windings in parallel and series connection, and connection method, high-speed performance, but the drive current is large (for motor winding current of 1.73 times), Connected in series when the drive current is equal to the motor winding current.
Five, the installation
- Around to have 20mm of space, can not be placed next to the other heating equipment, to avoid dust, oil mist,
Corrosive gases, high humidity is too big and strong vibration. +
Figure 3.
Six fault diagnosis
1, the status light indicates
RUN: green light in the normal work.
ERR: red light, power, light, power indicator
Size: 10.5x8.5x3.3cm(approx)

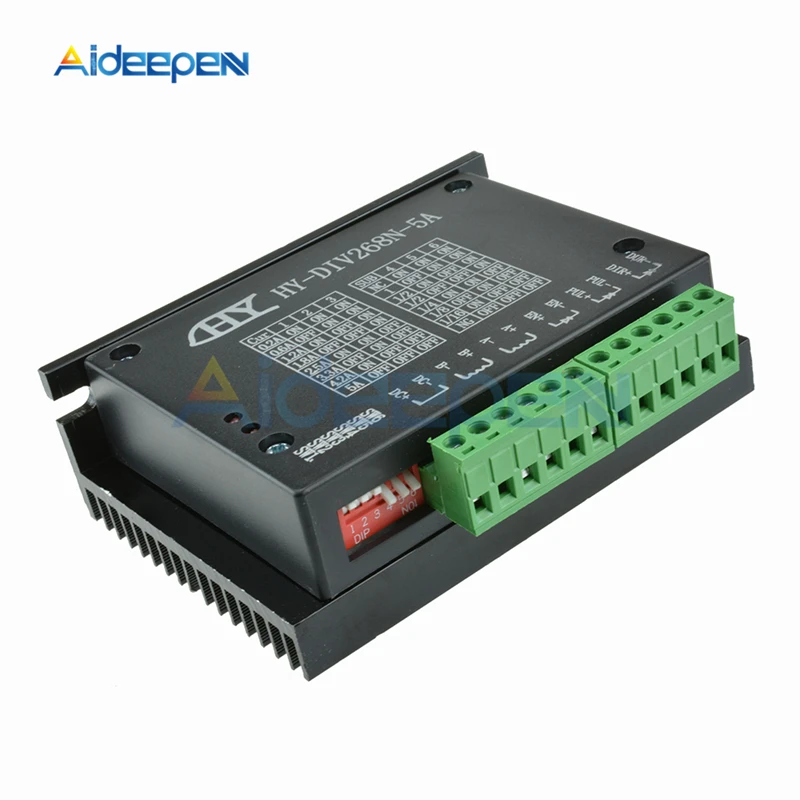
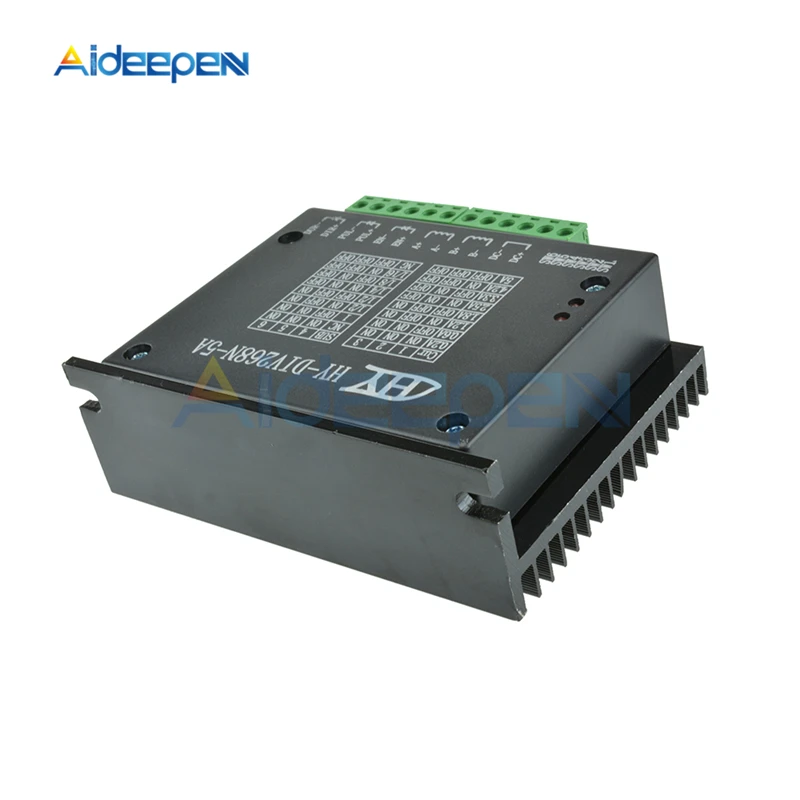

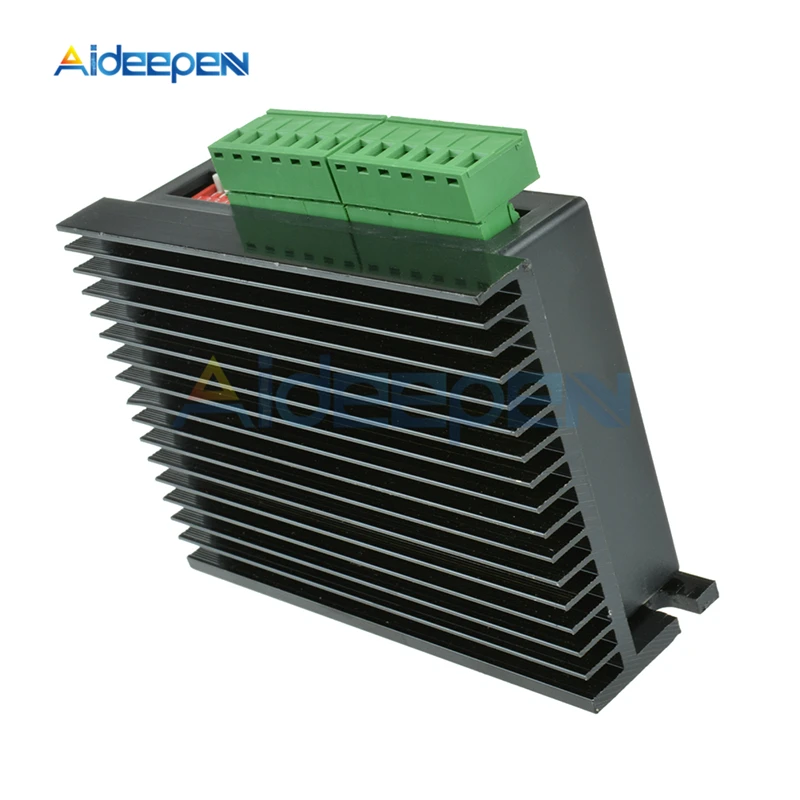
Purchasing & Delivery
Before you make your purchase, it’s helpful to know the measurements of the area you plan to place the furniture. You should also measure any doorways and hallways through which the furniture will pass to get to its final destination.Picking up at the store
Shopify Shop requires that all products are properly inspected BEFORE you take it home to insure there are no surprises. Our team is happy to open all packages and will assist in the inspection process. We will then reseal packages for safe transport. We encourage all customers to bring furniture pads or blankets to protect the items during transport as well as rope or tie downs. Shopify Shop will not be responsible for damage that occurs after leaving the store or during transit. It is the purchaser’s responsibility to make sure the correct items are picked up and in good condition.Delivery
Customers are able to pick the next available delivery day that best fits their schedule. However, to route stops as efficiently as possible, Shopify Shop will provide the time frame. Customers will not be able to choose a time. You will be notified in advance of your scheduled time frame. Please make sure that a responsible adult (18 years or older) will be home at that time.In preparation for your delivery, please remove existing furniture, pictures, mirrors, accessories, etc. to prevent damages. Also insure that the area where you would like your furniture placed is clear of any old furniture and any other items that may obstruct the passageway of the delivery team. Shopify Shop will deliver, assemble, and set-up your new furniture purchase and remove all packing materials from your home. Our delivery crews are not permitted to move your existing furniture or other household items. Delivery personnel will attempt to deliver the purchased items in a safe and controlled manner but will not attempt to place furniture if they feel it will result in damage to the product or your home. Delivery personnel are unable to remove doors, hoist furniture or carry furniture up more than 3 flights of stairs. An elevator must be available for deliveries to the 4th floor and above.
Other Customers also buy:
-
$5.99 USD{"id":4490370023495,"title":"4A 5A TB6600 Single Axis Stepper Motor Driver Controller Board CNC Engraving Machine 1 Axis Stepping Motor Driver Module","handle":"4a-5a-tb6600-single-axis-stepper-motor-driver-controller-board-cnc-engraving-machine-1-axis-stepping-motor-driver-module","description":"\u003cdiv class=\"detailmodule_text-image\"\u003e\n\u003cp class=\"detail-desc-decorate-title\" data-spm-anchor-id=\"a2g0o.detail.1000023.i0.18421cf5ZdYzqP\"\u003e\u003cstrong\u003e4A-TB6600\u003c\/strong\u003e\u003cbr\u003e\u003cbr\u003eSpecifications:\u003cbr\u003eSupply Voltage: 9~42VDC\u003cbr\u003eMax Drive Current: 4A\u003cbr\u003eChopping Frequency: 20KHZ\u003cbr\u003e \u003cbr\u003eFeatures:\u003cbr\u003eBipolar constant current chopper\u003cbr\u003eHigh-speed optocoupler signal isolation input\u003cbr\u003eElectrical input signal is TTL compatible\u003cbr\u003eStationary current is automatically reduced by half\u003c\/p\u003e\n\u003cimg src=\"https:\/\/ae01.alicdn.com\/kf\/Ha8b2526e84444ee9a78aea20742ee77e8.jpg\" class=\"detail-desc-decorate-image\"\u003e\u003cimg src=\"https:\/\/ae01.alicdn.com\/kf\/H839a8652f0184ef1b95d3dcffecbbc93W.jpg\" class=\"detail-desc-decorate-image\"\u003e\u003cimg src=\"https:\/\/ae01.alicdn.com\/kf\/Hbc427740876349ef8df4d15bec752e8dA.jpg\" class=\"detail-desc-decorate-image\"\u003e\n\u003c\/div\u003e\n\u003cdiv class=\"detailmodule_text-image\"\u003e\n\u003cp class=\"detail-desc-decorate-title\"\u003e\u003cstrong\u003e5A-TB6600\u003c\/strong\u003e\u003cbr\u003e\u003cbr\u003eHY-DIV268N-5A subdivision-type two-phase hybrid stepping motor drive using DC 12 ~ 48V power supply, suitable for drive\u003cbr\u003eTwo-phase hybrid stepping motor dynamic voltage 12 to 48V, the current is less than 5A outer diameter of 35 to 86 mm. This drive using the drive's current loop subdivision control, the motor torque ripple is very small, low-speed running is very smooth, almost no vibration and noise. High-speed torque is much higher than other two-phase drive, high positioning accuracy. Widely used in the engraving machine, CNC machine tools, packaging machinery and other high resolution requirements on the device.\u003cbr\u003e\u003cbr\u003eThe main features\u003cbr\u003e- average current control, two-phase sinusoidal current drive output\u003cbr\u003e- DC 12 ~ 48V power supply, the internal integration of 12V and 5V regulator\u003cbr\u003e- optically isolated signal input \/ output\u003cbr\u003e- overvoltage, undervoltage, overcurrent, and white short-circuit protection\u003cbr\u003e\u003cbr\u003e- Input voltage DC 12 ~ 48V input\u003cbr\u003e- The input current of 1 to 5 amps, select the drive a stepper motor.\u003cbr\u003e- Output current of 0.2A ~ 5A\u003cbr\u003e- Temperature Operating Temperature -10 to 45 ℃; Storage temperature -40 ℃ to 70 ℃\u003cbr\u003e- Humidity not condensing, not drops\u003cbr\u003e- Gas prohibit combustible gas and conductive dust\u003cbr\u003e- Weight 200 grams\u003cbr\u003e\u003cbr\u003eControl signal interface\u003cbr\u003e- Figure 1 is a wiring schematic of the drive\u003cbr\u003e- 1, the definition of control signals\u003cbr\u003ePUL +: step pulse signal is input side or the positive pulse signal input positive terminal\u003cbr\u003ePUL-: the negative input of the negative input pulse signal or a positive pulse signal\u003cbr\u003eDIR +: stepping direction signal input to the positive terminal or negative pulse signal input to the positive terminal\u003cbr\u003eDIR -: stepping direction signal input of the negative side or reverse step pulse signal input negative terminal\u003cbr\u003eEN +: offline can reset signal input side is\u003cbr\u003eEN-: offline can reset signal input negative terminal\u003cbr\u003eOffline enable signal is active, reset drive failure to prohibit any pulse, the output of the drive\u003cbr\u003ePower component is turned off, the motor holding torque.\u003cbr\u003e- Control signal connections\u003cbr\u003e- PC control signal can be high, also can be low effective. When active high, the control signal\u003cbr\u003e- The negative side together as a signal to active low, positive side of all control signals together as a signal common.\u003cbr\u003e- For example, open-collector and PNP output interface circuit diagram is as follows:\u003cbr\u003eFigure 2. Input interface circuit (common cathode connection)\u003cbr\u003e- Note: the VCC is 5V, R short;\u003cbr\u003e- VCC value of 12V, R 1K, more than 1\/8W resistor;\u003cbr\u003e- VCC value of 24V, R 2K, more than 1\/8W resistor;\u003cbr\u003e\u003cbr\u003eFunction selection (DIP switch on the drive panel)\u003cbr\u003e- Set the motor per revolution steps\u003cbr\u003eThe drive to set the number of steps per motor revolution is 200 (whole step), 400 (2 segments), 1600 (8 segments), 3200 steps (16 segments).\u003cbr\u003eThe user can drive the front panel DIP switch SW3 is SW4 bit of the drive to set the number of steps (such as Table 1):\u003cbr\u003eTable 1\u003cbr\u003e- Set the output phase current\u003cbr\u003e- To drive torque stepper motor, the user can drive panel DIP switch\u003cbr\u003e- SW1, SW2 is to set the drive output phase current (RMS) unit amperes, the switch position\u003cbr\u003e- Corresponding to the output current, output current value corresponding different types of drive. Concrete are shown in Table 2.\u003cbr\u003e- Output Current (A\u003cbr\u003eTable 2\u003cbr\u003eCurrent setting\u003cbr\u003e\u003cbr\u003e- the semi-flow functionality\u003cbr\u003e- The semi-flow function is a step pulse 200ms, the driver output current is automatically reduced to the rated output current50%, used to prevent motor heating.\u003cbr\u003eFourth, the power interface\u003cbr\u003e- 1, DC +, DC-: to connect the drive power\u003cbr\u003e- DC +: DC power level, power supply voltage DC 12 to 48V. The maximum current is 5A. The\u003cbr\u003eDC-: DC power supply negative level.\u003cbr\u003e2, A + A-B + B-: to connect the two-phase hybrid stepping motor\u003cbr\u003eDrive and two-phase hybrid stepper motor's connection with the four-wire system, the motor windings in parallel and series connection, and connection method, high-speed performance, but the drive current is large (for motor winding current of 1.73 times), Connected in series when the drive current is equal to the motor winding current.\u003cbr\u003eFive, the installation\u003cbr\u003e- Around to have 20mm of space, can not be placed next to the other heating equipment, to avoid dust, oil mist,\u003cbr\u003eCorrosive gases, high humidity is too big and strong vibration. +\u003cbr\u003eFigure 3.\u003cbr\u003eSix fault diagnosis\u003cbr\u003e1, the status light indicates\u003cbr\u003eRUN: green light in the normal work.\u003cbr\u003eERR: red light, power, light, power indicator\u003cbr\u003eSize: 10.5x8.5x3.3cm(approx)\u003c\/p\u003e\n\u003cimg src=\"https:\/\/ae01.alicdn.com\/kf\/He236654ff01e4461b3907273c5ea2dd0z.jpg\" class=\"detail-desc-decorate-image\"\u003e\u003cimg src=\"https:\/\/ae01.alicdn.com\/kf\/H77553a99bd4e46368cda2f21564c0af9p.jpg\" class=\"detail-desc-decorate-image\"\u003e\u003cimg src=\"https:\/\/ae01.alicdn.com\/kf\/Hc397f6a15fe8431bbcb8fe86468830fbk.jpg\" class=\"detail-desc-decorate-image\"\u003e\u003cimg src=\"https:\/\/ae01.alicdn.com\/kf\/Hc150b70a72af438d9ca4dea9bb464a43A.jpg\" class=\"detail-desc-decorate-image\"\u003e\u003cimg src=\"https:\/\/ae01.alicdn.com\/kf\/H2d60bfbea92d45ff9898a39239cf0c88d.jpg\" class=\"detail-desc-decorate-image\"\u003e\n\u003c\/div\u003e","published_at":"2020-02-19T21:25:58+08:00","created_at":"2020-02-19T21:41:01+08:00","vendor":"diymore","type":"Motor Speed Controller","tags":[],"price":1599,"price_min":1599,"price_max":1899,"available":true,"price_varies":true,"compare_at_price":null,"compare_at_price_min":0,"compare_at_price_max":0,"compare_at_price_varies":false,"variants":[{"id":31776718946375,"title":"5A-TB6600","option1":"5A-TB6600","option2":null,"option3":null,"sku":"010700","requires_shipping":true,"taxable":true,"featured_image":{"id":14509377224775,"product_id":4490370023495,"position":2,"created_at":"2020-05-06T01:56:08+08:00","updated_at":"2020-05-06T01:56:13+08:00","alt":"4A 5A Tb6600 Single Axis Stepper Motor Driver Controller Board Cnc Engraving Machine 1 Stepping","width":1000,"height":1000,"src":"\/\/www.diymore.cc\/cdn\/shop\/products\/He236654ff01e4461b3907273c5ea2dd0z_683.jpg?v=1588701373","variant_ids":[31776718946375]},"available":true,"name":"4A 5A TB6600 Single Axis Stepper Motor Driver Controller Board CNC Engraving Machine 1 Axis Stepping Motor Driver Module - 5A-TB6600","public_title":"5A-TB6600","options":["5A-TB6600"],"price":1899,"weight":0,"compare_at_price":null,"inventory_management":null,"barcode":"","featured_media":{"alt":"4A 5A Tb6600 Single Axis Stepper Motor Driver Controller Board Cnc Engraving Machine 1 Stepping","id":6682564100167,"position":2,"preview_image":{"aspect_ratio":1.0,"height":1000,"width":1000,"src":"\/\/www.diymore.cc\/cdn\/shop\/products\/He236654ff01e4461b3907273c5ea2dd0z_683.jpg?v=1588701373"}},"requires_selling_plan":false,"selling_plan_allocations":[]},{"id":31776718979143,"title":"4A-TB6600","option1":"4A-TB6600","option2":null,"option3":null,"sku":"010740","requires_shipping":true,"taxable":true,"featured_image":{"id":14509377650759,"product_id":4490370023495,"position":3,"created_at":"2020-05-06T01:56:12+08:00","updated_at":"2020-05-06T01:56:13+08:00","alt":"4A 5A Tb6600 Single Axis Stepper Motor Driver Controller Board Cnc Engraving Machine 1 Stepping","width":1000,"height":1000,"src":"\/\/www.diymore.cc\/cdn\/shop\/products\/Ha8b2526e84444ee9a78aea20742ee77e8_352.jpg?v=1588701373","variant_ids":[31776718979143]},"available":true,"name":"4A 5A TB6600 Single Axis Stepper Motor Driver Controller Board CNC Engraving Machine 1 Axis Stepping Motor Driver Module - 4A-TB6600","public_title":"4A-TB6600","options":["4A-TB6600"],"price":1599,"weight":0,"compare_at_price":null,"inventory_management":null,"barcode":"","featured_media":{"alt":"4A 5A Tb6600 Single Axis Stepper Motor Driver Controller Board Cnc Engraving Machine 1 Stepping","id":6682564427847,"position":3,"preview_image":{"aspect_ratio":1.0,"height":1000,"width":1000,"src":"\/\/www.diymore.cc\/cdn\/shop\/products\/Ha8b2526e84444ee9a78aea20742ee77e8_352.jpg?v=1588701373"}},"requires_selling_plan":false,"selling_plan_allocations":[]}],"images":["\/\/www.diymore.cc\/cdn\/shop\/products\/4A_5A_TB6600_Single_Axis_Stepper_Motor_Driver_Controller_Board_CNC_Engraving_Machine_1_Axis_Stepping_565.jpg?v=1588701373","\/\/www.diymore.cc\/cdn\/shop\/products\/He236654ff01e4461b3907273c5ea2dd0z_683.jpg?v=1588701373","\/\/www.diymore.cc\/cdn\/shop\/products\/Ha8b2526e84444ee9a78aea20742ee77e8_352.jpg?v=1588701373"],"featured_image":"\/\/www.diymore.cc\/cdn\/shop\/products\/4A_5A_TB6600_Single_Axis_Stepper_Motor_Driver_Controller_Board_CNC_Engraving_Machine_1_Axis_Stepping_565.jpg?v=1588701373","options":["Style"],"media":[{"alt":"4A 5A Tb6600 Single Axis Stepper Motor Driver Controller Board Cnc Engraving Machine 1 Stepping","id":6682563870791,"position":1,"preview_image":{"aspect_ratio":1.0,"height":1000,"width":1000,"src":"\/\/www.diymore.cc\/cdn\/shop\/products\/4A_5A_TB6600_Single_Axis_Stepper_Motor_Driver_Controller_Board_CNC_Engraving_Machine_1_Axis_Stepping_565.jpg?v=1588701373"},"aspect_ratio":1.0,"height":1000,"media_type":"image","src":"\/\/www.diymore.cc\/cdn\/shop\/products\/4A_5A_TB6600_Single_Axis_Stepper_Motor_Driver_Controller_Board_CNC_Engraving_Machine_1_Axis_Stepping_565.jpg?v=1588701373","width":1000},{"alt":"4A 5A Tb6600 Single Axis Stepper Motor Driver Controller Board Cnc Engraving Machine 1 Stepping","id":6682564100167,"position":2,"preview_image":{"aspect_ratio":1.0,"height":1000,"width":1000,"src":"\/\/www.diymore.cc\/cdn\/shop\/products\/He236654ff01e4461b3907273c5ea2dd0z_683.jpg?v=1588701373"},"aspect_ratio":1.0,"height":1000,"media_type":"image","src":"\/\/www.diymore.cc\/cdn\/shop\/products\/He236654ff01e4461b3907273c5ea2dd0z_683.jpg?v=1588701373","width":1000},{"alt":"4A 5A Tb6600 Single Axis Stepper Motor Driver Controller Board Cnc Engraving Machine 1 Stepping","id":6682564427847,"position":3,"preview_image":{"aspect_ratio":1.0,"height":1000,"width":1000,"src":"\/\/www.diymore.cc\/cdn\/shop\/products\/Ha8b2526e84444ee9a78aea20742ee77e8_352.jpg?v=1588701373"},"aspect_ratio":1.0,"height":1000,"media_type":"image","src":"\/\/www.diymore.cc\/cdn\/shop\/products\/Ha8b2526e84444ee9a78aea20742ee77e8_352.jpg?v=1588701373","width":1000}],"requires_selling_plan":false,"selling_plan_groups":[],"content":"\u003cdiv class=\"detailmodule_text-image\"\u003e\n\u003cp class=\"detail-desc-decorate-title\" data-spm-anchor-id=\"a2g0o.detail.1000023.i0.18421cf5ZdYzqP\"\u003e\u003cstrong\u003e4A-TB6600\u003c\/strong\u003e\u003cbr\u003e\u003cbr\u003eSpecifications:\u003cbr\u003eSupply Voltage: 9~42VDC\u003cbr\u003eMax Drive Current: 4A\u003cbr\u003eChopping Frequency: 20KHZ\u003cbr\u003e \u003cbr\u003eFeatures:\u003cbr\u003eBipolar constant current chopper\u003cbr\u003eHigh-speed optocoupler signal isolation input\u003cbr\u003eElectrical input signal is TTL compatible\u003cbr\u003eStationary current is automatically reduced by half\u003c\/p\u003e\n\u003cimg src=\"https:\/\/ae01.alicdn.com\/kf\/Ha8b2526e84444ee9a78aea20742ee77e8.jpg\" class=\"detail-desc-decorate-image\"\u003e\u003cimg src=\"https:\/\/ae01.alicdn.com\/kf\/H839a8652f0184ef1b95d3dcffecbbc93W.jpg\" class=\"detail-desc-decorate-image\"\u003e\u003cimg src=\"https:\/\/ae01.alicdn.com\/kf\/Hbc427740876349ef8df4d15bec752e8dA.jpg\" class=\"detail-desc-decorate-image\"\u003e\n\u003c\/div\u003e\n\u003cdiv class=\"detailmodule_text-image\"\u003e\n\u003cp class=\"detail-desc-decorate-title\"\u003e\u003cstrong\u003e5A-TB6600\u003c\/strong\u003e\u003cbr\u003e\u003cbr\u003eHY-DIV268N-5A subdivision-type two-phase hybrid stepping motor drive using DC 12 ~ 48V power supply, suitable for drive\u003cbr\u003eTwo-phase hybrid stepping motor dynamic voltage 12 to 48V, the current is less than 5A outer diameter of 35 to 86 mm. This drive using the drive's current loop subdivision control, the motor torque ripple is very small, low-speed running is very smooth, almost no vibration and noise. High-speed torque is much higher than other two-phase drive, high positioning accuracy. Widely used in the engraving machine, CNC machine tools, packaging machinery and other high resolution requirements on the device.\u003cbr\u003e\u003cbr\u003eThe main features\u003cbr\u003e- average current control, two-phase sinusoidal current drive output\u003cbr\u003e- DC 12 ~ 48V power supply, the internal integration of 12V and 5V regulator\u003cbr\u003e- optically isolated signal input \/ output\u003cbr\u003e- overvoltage, undervoltage, overcurrent, and white short-circuit protection\u003cbr\u003e\u003cbr\u003e- Input voltage DC 12 ~ 48V input\u003cbr\u003e- The input current of 1 to 5 amps, select the drive a stepper motor.\u003cbr\u003e- Output current of 0.2A ~ 5A\u003cbr\u003e- Temperature Operating Temperature -10 to 45 ℃; Storage temperature -40 ℃ to 70 ℃\u003cbr\u003e- Humidity not condensing, not drops\u003cbr\u003e- Gas prohibit combustible gas and conductive dust\u003cbr\u003e- Weight 200 grams\u003cbr\u003e\u003cbr\u003eControl signal interface\u003cbr\u003e- Figure 1 is a wiring schematic of the drive\u003cbr\u003e- 1, the definition of control signals\u003cbr\u003ePUL +: step pulse signal is input side or the positive pulse signal input positive terminal\u003cbr\u003ePUL-: the negative input of the negative input pulse signal or a positive pulse signal\u003cbr\u003eDIR +: stepping direction signal input to the positive terminal or negative pulse signal input to the positive terminal\u003cbr\u003eDIR -: stepping direction signal input of the negative side or reverse step pulse signal input negative terminal\u003cbr\u003eEN +: offline can reset signal input side is\u003cbr\u003eEN-: offline can reset signal input negative terminal\u003cbr\u003eOffline enable signal is active, reset drive failure to prohibit any pulse, the output of the drive\u003cbr\u003ePower component is turned off, the motor holding torque.\u003cbr\u003e- Control signal connections\u003cbr\u003e- PC control signal can be high, also can be low effective. When active high, the control signal\u003cbr\u003e- The negative side together as a signal to active low, positive side of all control signals together as a signal common.\u003cbr\u003e- For example, open-collector and PNP output interface circuit diagram is as follows:\u003cbr\u003eFigure 2. Input interface circuit (common cathode connection)\u003cbr\u003e- Note: the VCC is 5V, R short;\u003cbr\u003e- VCC value of 12V, R 1K, more than 1\/8W resistor;\u003cbr\u003e- VCC value of 24V, R 2K, more than 1\/8W resistor;\u003cbr\u003e\u003cbr\u003eFunction selection (DIP switch on the drive panel)\u003cbr\u003e- Set the motor per revolution steps\u003cbr\u003eThe drive to set the number of steps per motor revolution is 200 (whole step), 400 (2 segments), 1600 (8 segments), 3200 steps (16 segments).\u003cbr\u003eThe user can drive the front panel DIP switch SW3 is SW4 bit of the drive to set the number of steps (such as Table 1):\u003cbr\u003eTable 1\u003cbr\u003e- Set the output phase current\u003cbr\u003e- To drive torque stepper motor, the user can drive panel DIP switch\u003cbr\u003e- SW1, SW2 is to set the drive output phase current (RMS) unit amperes, the switch position\u003cbr\u003e- Corresponding to the output current, output current value corresponding different types of drive. Concrete are shown in Table 2.\u003cbr\u003e- Output Current (A\u003cbr\u003eTable 2\u003cbr\u003eCurrent setting\u003cbr\u003e\u003cbr\u003e- the semi-flow functionality\u003cbr\u003e- The semi-flow function is a step pulse 200ms, the driver output current is automatically reduced to the rated output current50%, used to prevent motor heating.\u003cbr\u003eFourth, the power interface\u003cbr\u003e- 1, DC +, DC-: to connect the drive power\u003cbr\u003e- DC +: DC power level, power supply voltage DC 12 to 48V. The maximum current is 5A. The\u003cbr\u003eDC-: DC power supply negative level.\u003cbr\u003e2, A + A-B + B-: to connect the two-phase hybrid stepping motor\u003cbr\u003eDrive and two-phase hybrid stepper motor's connection with the four-wire system, the motor windings in parallel and series connection, and connection method, high-speed performance, but the drive current is large (for motor winding current of 1.73 times), Connected in series when the drive current is equal to the motor winding current.\u003cbr\u003eFive, the installation\u003cbr\u003e- Around to have 20mm of space, can not be placed next to the other heating equipment, to avoid dust, oil mist,\u003cbr\u003eCorrosive gases, high humidity is too big and strong vibration. +\u003cbr\u003eFigure 3.\u003cbr\u003eSix fault diagnosis\u003cbr\u003e1, the status light indicates\u003cbr\u003eRUN: green light in the normal work.\u003cbr\u003eERR: red light, power, light, power indicator\u003cbr\u003eSize: 10.5x8.5x3.3cm(approx)\u003c\/p\u003e\n\u003cimg src=\"https:\/\/ae01.alicdn.com\/kf\/He236654ff01e4461b3907273c5ea2dd0z.jpg\" class=\"detail-desc-decorate-image\"\u003e\u003cimg src=\"https:\/\/ae01.alicdn.com\/kf\/H77553a99bd4e46368cda2f21564c0af9p.jpg\" class=\"detail-desc-decorate-image\"\u003e\u003cimg src=\"https:\/\/ae01.alicdn.com\/kf\/Hc397f6a15fe8431bbcb8fe86468830fbk.jpg\" class=\"detail-desc-decorate-image\"\u003e\u003cimg src=\"https:\/\/ae01.alicdn.com\/kf\/Hc150b70a72af438d9ca4dea9bb464a43A.jpg\" class=\"detail-desc-decorate-image\"\u003e\u003cimg src=\"https:\/\/ae01.alicdn.com\/kf\/H2d60bfbea92d45ff9898a39239cf0c88d.jpg\" class=\"detail-desc-decorate-image\"\u003e\n\u003c\/div\u003e"}
-
$8.99 USD{"id":4490370023495,"title":"4A 5A TB6600 Single Axis Stepper Motor Driver Controller Board CNC Engraving Machine 1 Axis Stepping Motor Driver Module","handle":"4a-5a-tb6600-single-axis-stepper-motor-driver-controller-board-cnc-engraving-machine-1-axis-stepping-motor-driver-module","description":"\u003cdiv class=\"detailmodule_text-image\"\u003e\n\u003cp class=\"detail-desc-decorate-title\" data-spm-anchor-id=\"a2g0o.detail.1000023.i0.18421cf5ZdYzqP\"\u003e\u003cstrong\u003e4A-TB6600\u003c\/strong\u003e\u003cbr\u003e\u003cbr\u003eSpecifications:\u003cbr\u003eSupply Voltage: 9~42VDC\u003cbr\u003eMax Drive Current: 4A\u003cbr\u003eChopping Frequency: 20KHZ\u003cbr\u003e \u003cbr\u003eFeatures:\u003cbr\u003eBipolar constant current chopper\u003cbr\u003eHigh-speed optocoupler signal isolation input\u003cbr\u003eElectrical input signal is TTL compatible\u003cbr\u003eStationary current is automatically reduced by half\u003c\/p\u003e\n\u003cimg src=\"https:\/\/ae01.alicdn.com\/kf\/Ha8b2526e84444ee9a78aea20742ee77e8.jpg\" class=\"detail-desc-decorate-image\"\u003e\u003cimg src=\"https:\/\/ae01.alicdn.com\/kf\/H839a8652f0184ef1b95d3dcffecbbc93W.jpg\" class=\"detail-desc-decorate-image\"\u003e\u003cimg src=\"https:\/\/ae01.alicdn.com\/kf\/Hbc427740876349ef8df4d15bec752e8dA.jpg\" class=\"detail-desc-decorate-image\"\u003e\n\u003c\/div\u003e\n\u003cdiv class=\"detailmodule_text-image\"\u003e\n\u003cp class=\"detail-desc-decorate-title\"\u003e\u003cstrong\u003e5A-TB6600\u003c\/strong\u003e\u003cbr\u003e\u003cbr\u003eHY-DIV268N-5A subdivision-type two-phase hybrid stepping motor drive using DC 12 ~ 48V power supply, suitable for drive\u003cbr\u003eTwo-phase hybrid stepping motor dynamic voltage 12 to 48V, the current is less than 5A outer diameter of 35 to 86 mm. This drive using the drive's current loop subdivision control, the motor torque ripple is very small, low-speed running is very smooth, almost no vibration and noise. High-speed torque is much higher than other two-phase drive, high positioning accuracy. Widely used in the engraving machine, CNC machine tools, packaging machinery and other high resolution requirements on the device.\u003cbr\u003e\u003cbr\u003eThe main features\u003cbr\u003e- average current control, two-phase sinusoidal current drive output\u003cbr\u003e- DC 12 ~ 48V power supply, the internal integration of 12V and 5V regulator\u003cbr\u003e- optically isolated signal input \/ output\u003cbr\u003e- overvoltage, undervoltage, overcurrent, and white short-circuit protection\u003cbr\u003e\u003cbr\u003e- Input voltage DC 12 ~ 48V input\u003cbr\u003e- The input current of 1 to 5 amps, select the drive a stepper motor.\u003cbr\u003e- Output current of 0.2A ~ 5A\u003cbr\u003e- Temperature Operating Temperature -10 to 45 ℃; Storage temperature -40 ℃ to 70 ℃\u003cbr\u003e- Humidity not condensing, not drops\u003cbr\u003e- Gas prohibit combustible gas and conductive dust\u003cbr\u003e- Weight 200 grams\u003cbr\u003e\u003cbr\u003eControl signal interface\u003cbr\u003e- Figure 1 is a wiring schematic of the drive\u003cbr\u003e- 1, the definition of control signals\u003cbr\u003ePUL +: step pulse signal is input side or the positive pulse signal input positive terminal\u003cbr\u003ePUL-: the negative input of the negative input pulse signal or a positive pulse signal\u003cbr\u003eDIR +: stepping direction signal input to the positive terminal or negative pulse signal input to the positive terminal\u003cbr\u003eDIR -: stepping direction signal input of the negative side or reverse step pulse signal input negative terminal\u003cbr\u003eEN +: offline can reset signal input side is\u003cbr\u003eEN-: offline can reset signal input negative terminal\u003cbr\u003eOffline enable signal is active, reset drive failure to prohibit any pulse, the output of the drive\u003cbr\u003ePower component is turned off, the motor holding torque.\u003cbr\u003e- Control signal connections\u003cbr\u003e- PC control signal can be high, also can be low effective. When active high, the control signal\u003cbr\u003e- The negative side together as a signal to active low, positive side of all control signals together as a signal common.\u003cbr\u003e- For example, open-collector and PNP output interface circuit diagram is as follows:\u003cbr\u003eFigure 2. Input interface circuit (common cathode connection)\u003cbr\u003e- Note: the VCC is 5V, R short;\u003cbr\u003e- VCC value of 12V, R 1K, more than 1\/8W resistor;\u003cbr\u003e- VCC value of 24V, R 2K, more than 1\/8W resistor;\u003cbr\u003e\u003cbr\u003eFunction selection (DIP switch on the drive panel)\u003cbr\u003e- Set the motor per revolution steps\u003cbr\u003eThe drive to set the number of steps per motor revolution is 200 (whole step), 400 (2 segments), 1600 (8 segments), 3200 steps (16 segments).\u003cbr\u003eThe user can drive the front panel DIP switch SW3 is SW4 bit of the drive to set the number of steps (such as Table 1):\u003cbr\u003eTable 1\u003cbr\u003e- Set the output phase current\u003cbr\u003e- To drive torque stepper motor, the user can drive panel DIP switch\u003cbr\u003e- SW1, SW2 is to set the drive output phase current (RMS) unit amperes, the switch position\u003cbr\u003e- Corresponding to the output current, output current value corresponding different types of drive. Concrete are shown in Table 2.\u003cbr\u003e- Output Current (A\u003cbr\u003eTable 2\u003cbr\u003eCurrent setting\u003cbr\u003e\u003cbr\u003e- the semi-flow functionality\u003cbr\u003e- The semi-flow function is a step pulse 200ms, the driver output current is automatically reduced to the rated output current50%, used to prevent motor heating.\u003cbr\u003eFourth, the power interface\u003cbr\u003e- 1, DC +, DC-: to connect the drive power\u003cbr\u003e- DC +: DC power level, power supply voltage DC 12 to 48V. The maximum current is 5A. The\u003cbr\u003eDC-: DC power supply negative level.\u003cbr\u003e2, A + A-B + B-: to connect the two-phase hybrid stepping motor\u003cbr\u003eDrive and two-phase hybrid stepper motor's connection with the four-wire system, the motor windings in parallel and series connection, and connection method, high-speed performance, but the drive current is large (for motor winding current of 1.73 times), Connected in series when the drive current is equal to the motor winding current.\u003cbr\u003eFive, the installation\u003cbr\u003e- Around to have 20mm of space, can not be placed next to the other heating equipment, to avoid dust, oil mist,\u003cbr\u003eCorrosive gases, high humidity is too big and strong vibration. +\u003cbr\u003eFigure 3.\u003cbr\u003eSix fault diagnosis\u003cbr\u003e1, the status light indicates\u003cbr\u003eRUN: green light in the normal work.\u003cbr\u003eERR: red light, power, light, power indicator\u003cbr\u003eSize: 10.5x8.5x3.3cm(approx)\u003c\/p\u003e\n\u003cimg src=\"https:\/\/ae01.alicdn.com\/kf\/He236654ff01e4461b3907273c5ea2dd0z.jpg\" class=\"detail-desc-decorate-image\"\u003e\u003cimg src=\"https:\/\/ae01.alicdn.com\/kf\/H77553a99bd4e46368cda2f21564c0af9p.jpg\" class=\"detail-desc-decorate-image\"\u003e\u003cimg src=\"https:\/\/ae01.alicdn.com\/kf\/Hc397f6a15fe8431bbcb8fe86468830fbk.jpg\" class=\"detail-desc-decorate-image\"\u003e\u003cimg src=\"https:\/\/ae01.alicdn.com\/kf\/Hc150b70a72af438d9ca4dea9bb464a43A.jpg\" class=\"detail-desc-decorate-image\"\u003e\u003cimg src=\"https:\/\/ae01.alicdn.com\/kf\/H2d60bfbea92d45ff9898a39239cf0c88d.jpg\" class=\"detail-desc-decorate-image\"\u003e\n\u003c\/div\u003e","published_at":"2020-02-19T21:25:58+08:00","created_at":"2020-02-19T21:41:01+08:00","vendor":"diymore","type":"Motor Speed Controller","tags":[],"price":1599,"price_min":1599,"price_max":1899,"available":true,"price_varies":true,"compare_at_price":null,"compare_at_price_min":0,"compare_at_price_max":0,"compare_at_price_varies":false,"variants":[{"id":31776718946375,"title":"5A-TB6600","option1":"5A-TB6600","option2":null,"option3":null,"sku":"010700","requires_shipping":true,"taxable":true,"featured_image":{"id":14509377224775,"product_id":4490370023495,"position":2,"created_at":"2020-05-06T01:56:08+08:00","updated_at":"2020-05-06T01:56:13+08:00","alt":"4A 5A Tb6600 Single Axis Stepper Motor Driver Controller Board Cnc Engraving Machine 1 Stepping","width":1000,"height":1000,"src":"\/\/www.diymore.cc\/cdn\/shop\/products\/He236654ff01e4461b3907273c5ea2dd0z_683.jpg?v=1588701373","variant_ids":[31776718946375]},"available":true,"name":"4A 5A TB6600 Single Axis Stepper Motor Driver Controller Board CNC Engraving Machine 1 Axis Stepping Motor Driver Module - 5A-TB6600","public_title":"5A-TB6600","options":["5A-TB6600"],"price":1899,"weight":0,"compare_at_price":null,"inventory_management":null,"barcode":"","featured_media":{"alt":"4A 5A Tb6600 Single Axis Stepper Motor Driver Controller Board Cnc Engraving Machine 1 Stepping","id":6682564100167,"position":2,"preview_image":{"aspect_ratio":1.0,"height":1000,"width":1000,"src":"\/\/www.diymore.cc\/cdn\/shop\/products\/He236654ff01e4461b3907273c5ea2dd0z_683.jpg?v=1588701373"}},"requires_selling_plan":false,"selling_plan_allocations":[]},{"id":31776718979143,"title":"4A-TB6600","option1":"4A-TB6600","option2":null,"option3":null,"sku":"010740","requires_shipping":true,"taxable":true,"featured_image":{"id":14509377650759,"product_id":4490370023495,"position":3,"created_at":"2020-05-06T01:56:12+08:00","updated_at":"2020-05-06T01:56:13+08:00","alt":"4A 5A Tb6600 Single Axis Stepper Motor Driver Controller Board Cnc Engraving Machine 1 Stepping","width":1000,"height":1000,"src":"\/\/www.diymore.cc\/cdn\/shop\/products\/Ha8b2526e84444ee9a78aea20742ee77e8_352.jpg?v=1588701373","variant_ids":[31776718979143]},"available":true,"name":"4A 5A TB6600 Single Axis Stepper Motor Driver Controller Board CNC Engraving Machine 1 Axis Stepping Motor Driver Module - 4A-TB6600","public_title":"4A-TB6600","options":["4A-TB6600"],"price":1599,"weight":0,"compare_at_price":null,"inventory_management":null,"barcode":"","featured_media":{"alt":"4A 5A Tb6600 Single Axis Stepper Motor Driver Controller Board Cnc Engraving Machine 1 Stepping","id":6682564427847,"position":3,"preview_image":{"aspect_ratio":1.0,"height":1000,"width":1000,"src":"\/\/www.diymore.cc\/cdn\/shop\/products\/Ha8b2526e84444ee9a78aea20742ee77e8_352.jpg?v=1588701373"}},"requires_selling_plan":false,"selling_plan_allocations":[]}],"images":["\/\/www.diymore.cc\/cdn\/shop\/products\/4A_5A_TB6600_Single_Axis_Stepper_Motor_Driver_Controller_Board_CNC_Engraving_Machine_1_Axis_Stepping_565.jpg?v=1588701373","\/\/www.diymore.cc\/cdn\/shop\/products\/He236654ff01e4461b3907273c5ea2dd0z_683.jpg?v=1588701373","\/\/www.diymore.cc\/cdn\/shop\/products\/Ha8b2526e84444ee9a78aea20742ee77e8_352.jpg?v=1588701373"],"featured_image":"\/\/www.diymore.cc\/cdn\/shop\/products\/4A_5A_TB6600_Single_Axis_Stepper_Motor_Driver_Controller_Board_CNC_Engraving_Machine_1_Axis_Stepping_565.jpg?v=1588701373","options":["Style"],"media":[{"alt":"4A 5A Tb6600 Single Axis Stepper Motor Driver Controller Board Cnc Engraving Machine 1 Stepping","id":6682563870791,"position":1,"preview_image":{"aspect_ratio":1.0,"height":1000,"width":1000,"src":"\/\/www.diymore.cc\/cdn\/shop\/products\/4A_5A_TB6600_Single_Axis_Stepper_Motor_Driver_Controller_Board_CNC_Engraving_Machine_1_Axis_Stepping_565.jpg?v=1588701373"},"aspect_ratio":1.0,"height":1000,"media_type":"image","src":"\/\/www.diymore.cc\/cdn\/shop\/products\/4A_5A_TB6600_Single_Axis_Stepper_Motor_Driver_Controller_Board_CNC_Engraving_Machine_1_Axis_Stepping_565.jpg?v=1588701373","width":1000},{"alt":"4A 5A Tb6600 Single Axis Stepper Motor Driver Controller Board Cnc Engraving Machine 1 Stepping","id":6682564100167,"position":2,"preview_image":{"aspect_ratio":1.0,"height":1000,"width":1000,"src":"\/\/www.diymore.cc\/cdn\/shop\/products\/He236654ff01e4461b3907273c5ea2dd0z_683.jpg?v=1588701373"},"aspect_ratio":1.0,"height":1000,"media_type":"image","src":"\/\/www.diymore.cc\/cdn\/shop\/products\/He236654ff01e4461b3907273c5ea2dd0z_683.jpg?v=1588701373","width":1000},{"alt":"4A 5A Tb6600 Single Axis Stepper Motor Driver Controller Board Cnc Engraving Machine 1 Stepping","id":6682564427847,"position":3,"preview_image":{"aspect_ratio":1.0,"height":1000,"width":1000,"src":"\/\/www.diymore.cc\/cdn\/shop\/products\/Ha8b2526e84444ee9a78aea20742ee77e8_352.jpg?v=1588701373"},"aspect_ratio":1.0,"height":1000,"media_type":"image","src":"\/\/www.diymore.cc\/cdn\/shop\/products\/Ha8b2526e84444ee9a78aea20742ee77e8_352.jpg?v=1588701373","width":1000}],"requires_selling_plan":false,"selling_plan_groups":[],"content":"\u003cdiv class=\"detailmodule_text-image\"\u003e\n\u003cp class=\"detail-desc-decorate-title\" data-spm-anchor-id=\"a2g0o.detail.1000023.i0.18421cf5ZdYzqP\"\u003e\u003cstrong\u003e4A-TB6600\u003c\/strong\u003e\u003cbr\u003e\u003cbr\u003eSpecifications:\u003cbr\u003eSupply Voltage: 9~42VDC\u003cbr\u003eMax Drive Current: 4A\u003cbr\u003eChopping Frequency: 20KHZ\u003cbr\u003e \u003cbr\u003eFeatures:\u003cbr\u003eBipolar constant current chopper\u003cbr\u003eHigh-speed optocoupler signal isolation input\u003cbr\u003eElectrical input signal is TTL compatible\u003cbr\u003eStationary current is automatically reduced by half\u003c\/p\u003e\n\u003cimg src=\"https:\/\/ae01.alicdn.com\/kf\/Ha8b2526e84444ee9a78aea20742ee77e8.jpg\" class=\"detail-desc-decorate-image\"\u003e\u003cimg src=\"https:\/\/ae01.alicdn.com\/kf\/H839a8652f0184ef1b95d3dcffecbbc93W.jpg\" class=\"detail-desc-decorate-image\"\u003e\u003cimg src=\"https:\/\/ae01.alicdn.com\/kf\/Hbc427740876349ef8df4d15bec752e8dA.jpg\" class=\"detail-desc-decorate-image\"\u003e\n\u003c\/div\u003e\n\u003cdiv class=\"detailmodule_text-image\"\u003e\n\u003cp class=\"detail-desc-decorate-title\"\u003e\u003cstrong\u003e5A-TB6600\u003c\/strong\u003e\u003cbr\u003e\u003cbr\u003eHY-DIV268N-5A subdivision-type two-phase hybrid stepping motor drive using DC 12 ~ 48V power supply, suitable for drive\u003cbr\u003eTwo-phase hybrid stepping motor dynamic voltage 12 to 48V, the current is less than 5A outer diameter of 35 to 86 mm. This drive using the drive's current loop subdivision control, the motor torque ripple is very small, low-speed running is very smooth, almost no vibration and noise. High-speed torque is much higher than other two-phase drive, high positioning accuracy. Widely used in the engraving machine, CNC machine tools, packaging machinery and other high resolution requirements on the device.\u003cbr\u003e\u003cbr\u003eThe main features\u003cbr\u003e- average current control, two-phase sinusoidal current drive output\u003cbr\u003e- DC 12 ~ 48V power supply, the internal integration of 12V and 5V regulator\u003cbr\u003e- optically isolated signal input \/ output\u003cbr\u003e- overvoltage, undervoltage, overcurrent, and white short-circuit protection\u003cbr\u003e\u003cbr\u003e- Input voltage DC 12 ~ 48V input\u003cbr\u003e- The input current of 1 to 5 amps, select the drive a stepper motor.\u003cbr\u003e- Output current of 0.2A ~ 5A\u003cbr\u003e- Temperature Operating Temperature -10 to 45 ℃; Storage temperature -40 ℃ to 70 ℃\u003cbr\u003e- Humidity not condensing, not drops\u003cbr\u003e- Gas prohibit combustible gas and conductive dust\u003cbr\u003e- Weight 200 grams\u003cbr\u003e\u003cbr\u003eControl signal interface\u003cbr\u003e- Figure 1 is a wiring schematic of the drive\u003cbr\u003e- 1, the definition of control signals\u003cbr\u003ePUL +: step pulse signal is input side or the positive pulse signal input positive terminal\u003cbr\u003ePUL-: the negative input of the negative input pulse signal or a positive pulse signal\u003cbr\u003eDIR +: stepping direction signal input to the positive terminal or negative pulse signal input to the positive terminal\u003cbr\u003eDIR -: stepping direction signal input of the negative side or reverse step pulse signal input negative terminal\u003cbr\u003eEN +: offline can reset signal input side is\u003cbr\u003eEN-: offline can reset signal input negative terminal\u003cbr\u003eOffline enable signal is active, reset drive failure to prohibit any pulse, the output of the drive\u003cbr\u003ePower component is turned off, the motor holding torque.\u003cbr\u003e- Control signal connections\u003cbr\u003e- PC control signal can be high, also can be low effective. When active high, the control signal\u003cbr\u003e- The negative side together as a signal to active low, positive side of all control signals together as a signal common.\u003cbr\u003e- For example, open-collector and PNP output interface circuit diagram is as follows:\u003cbr\u003eFigure 2. Input interface circuit (common cathode connection)\u003cbr\u003e- Note: the VCC is 5V, R short;\u003cbr\u003e- VCC value of 12V, R 1K, more than 1\/8W resistor;\u003cbr\u003e- VCC value of 24V, R 2K, more than 1\/8W resistor;\u003cbr\u003e\u003cbr\u003eFunction selection (DIP switch on the drive panel)\u003cbr\u003e- Set the motor per revolution steps\u003cbr\u003eThe drive to set the number of steps per motor revolution is 200 (whole step), 400 (2 segments), 1600 (8 segments), 3200 steps (16 segments).\u003cbr\u003eThe user can drive the front panel DIP switch SW3 is SW4 bit of the drive to set the number of steps (such as Table 1):\u003cbr\u003eTable 1\u003cbr\u003e- Set the output phase current\u003cbr\u003e- To drive torque stepper motor, the user can drive panel DIP switch\u003cbr\u003e- SW1, SW2 is to set the drive output phase current (RMS) unit amperes, the switch position\u003cbr\u003e- Corresponding to the output current, output current value corresponding different types of drive. Concrete are shown in Table 2.\u003cbr\u003e- Output Current (A\u003cbr\u003eTable 2\u003cbr\u003eCurrent setting\u003cbr\u003e\u003cbr\u003e- the semi-flow functionality\u003cbr\u003e- The semi-flow function is a step pulse 200ms, the driver output current is automatically reduced to the rated output current50%, used to prevent motor heating.\u003cbr\u003eFourth, the power interface\u003cbr\u003e- 1, DC +, DC-: to connect the drive power\u003cbr\u003e- DC +: DC power level, power supply voltage DC 12 to 48V. The maximum current is 5A. The\u003cbr\u003eDC-: DC power supply negative level.\u003cbr\u003e2, A + A-B + B-: to connect the two-phase hybrid stepping motor\u003cbr\u003eDrive and two-phase hybrid stepper motor's connection with the four-wire system, the motor windings in parallel and series connection, and connection method, high-speed performance, but the drive current is large (for motor winding current of 1.73 times), Connected in series when the drive current is equal to the motor winding current.\u003cbr\u003eFive, the installation\u003cbr\u003e- Around to have 20mm of space, can not be placed next to the other heating equipment, to avoid dust, oil mist,\u003cbr\u003eCorrosive gases, high humidity is too big and strong vibration. +\u003cbr\u003eFigure 3.\u003cbr\u003eSix fault diagnosis\u003cbr\u003e1, the status light indicates\u003cbr\u003eRUN: green light in the normal work.\u003cbr\u003eERR: red light, power, light, power indicator\u003cbr\u003eSize: 10.5x8.5x3.3cm(approx)\u003c\/p\u003e\n\u003cimg src=\"https:\/\/ae01.alicdn.com\/kf\/He236654ff01e4461b3907273c5ea2dd0z.jpg\" class=\"detail-desc-decorate-image\"\u003e\u003cimg src=\"https:\/\/ae01.alicdn.com\/kf\/H77553a99bd4e46368cda2f21564c0af9p.jpg\" class=\"detail-desc-decorate-image\"\u003e\u003cimg src=\"https:\/\/ae01.alicdn.com\/kf\/Hc397f6a15fe8431bbcb8fe86468830fbk.jpg\" class=\"detail-desc-decorate-image\"\u003e\u003cimg src=\"https:\/\/ae01.alicdn.com\/kf\/Hc150b70a72af438d9ca4dea9bb464a43A.jpg\" class=\"detail-desc-decorate-image\"\u003e\u003cimg src=\"https:\/\/ae01.alicdn.com\/kf\/H2d60bfbea92d45ff9898a39239cf0c88d.jpg\" class=\"detail-desc-decorate-image\"\u003e\n\u003c\/div\u003e"}
-
$16.99 USD{"id":4490370023495,"title":"4A 5A TB6600 Single Axis Stepper Motor Driver Controller Board CNC Engraving Machine 1 Axis Stepping Motor Driver Module","handle":"4a-5a-tb6600-single-axis-stepper-motor-driver-controller-board-cnc-engraving-machine-1-axis-stepping-motor-driver-module","description":"\u003cdiv class=\"detailmodule_text-image\"\u003e\n\u003cp class=\"detail-desc-decorate-title\" data-spm-anchor-id=\"a2g0o.detail.1000023.i0.18421cf5ZdYzqP\"\u003e\u003cstrong\u003e4A-TB6600\u003c\/strong\u003e\u003cbr\u003e\u003cbr\u003eSpecifications:\u003cbr\u003eSupply Voltage: 9~42VDC\u003cbr\u003eMax Drive Current: 4A\u003cbr\u003eChopping Frequency: 20KHZ\u003cbr\u003e \u003cbr\u003eFeatures:\u003cbr\u003eBipolar constant current chopper\u003cbr\u003eHigh-speed optocoupler signal isolation input\u003cbr\u003eElectrical input signal is TTL compatible\u003cbr\u003eStationary current is automatically reduced by half\u003c\/p\u003e\n\u003cimg src=\"https:\/\/ae01.alicdn.com\/kf\/Ha8b2526e84444ee9a78aea20742ee77e8.jpg\" class=\"detail-desc-decorate-image\"\u003e\u003cimg src=\"https:\/\/ae01.alicdn.com\/kf\/H839a8652f0184ef1b95d3dcffecbbc93W.jpg\" class=\"detail-desc-decorate-image\"\u003e\u003cimg src=\"https:\/\/ae01.alicdn.com\/kf\/Hbc427740876349ef8df4d15bec752e8dA.jpg\" class=\"detail-desc-decorate-image\"\u003e\n\u003c\/div\u003e\n\u003cdiv class=\"detailmodule_text-image\"\u003e\n\u003cp class=\"detail-desc-decorate-title\"\u003e\u003cstrong\u003e5A-TB6600\u003c\/strong\u003e\u003cbr\u003e\u003cbr\u003eHY-DIV268N-5A subdivision-type two-phase hybrid stepping motor drive using DC 12 ~ 48V power supply, suitable for drive\u003cbr\u003eTwo-phase hybrid stepping motor dynamic voltage 12 to 48V, the current is less than 5A outer diameter of 35 to 86 mm. This drive using the drive's current loop subdivision control, the motor torque ripple is very small, low-speed running is very smooth, almost no vibration and noise. High-speed torque is much higher than other two-phase drive, high positioning accuracy. Widely used in the engraving machine, CNC machine tools, packaging machinery and other high resolution requirements on the device.\u003cbr\u003e\u003cbr\u003eThe main features\u003cbr\u003e- average current control, two-phase sinusoidal current drive output\u003cbr\u003e- DC 12 ~ 48V power supply, the internal integration of 12V and 5V regulator\u003cbr\u003e- optically isolated signal input \/ output\u003cbr\u003e- overvoltage, undervoltage, overcurrent, and white short-circuit protection\u003cbr\u003e\u003cbr\u003e- Input voltage DC 12 ~ 48V input\u003cbr\u003e- The input current of 1 to 5 amps, select the drive a stepper motor.\u003cbr\u003e- Output current of 0.2A ~ 5A\u003cbr\u003e- Temperature Operating Temperature -10 to 45 ℃; Storage temperature -40 ℃ to 70 ℃\u003cbr\u003e- Humidity not condensing, not drops\u003cbr\u003e- Gas prohibit combustible gas and conductive dust\u003cbr\u003e- Weight 200 grams\u003cbr\u003e\u003cbr\u003eControl signal interface\u003cbr\u003e- Figure 1 is a wiring schematic of the drive\u003cbr\u003e- 1, the definition of control signals\u003cbr\u003ePUL +: step pulse signal is input side or the positive pulse signal input positive terminal\u003cbr\u003ePUL-: the negative input of the negative input pulse signal or a positive pulse signal\u003cbr\u003eDIR +: stepping direction signal input to the positive terminal or negative pulse signal input to the positive terminal\u003cbr\u003eDIR -: stepping direction signal input of the negative side or reverse step pulse signal input negative terminal\u003cbr\u003eEN +: offline can reset signal input side is\u003cbr\u003eEN-: offline can reset signal input negative terminal\u003cbr\u003eOffline enable signal is active, reset drive failure to prohibit any pulse, the output of the drive\u003cbr\u003ePower component is turned off, the motor holding torque.\u003cbr\u003e- Control signal connections\u003cbr\u003e- PC control signal can be high, also can be low effective. When active high, the control signal\u003cbr\u003e- The negative side together as a signal to active low, positive side of all control signals together as a signal common.\u003cbr\u003e- For example, open-collector and PNP output interface circuit diagram is as follows:\u003cbr\u003eFigure 2. Input interface circuit (common cathode connection)\u003cbr\u003e- Note: the VCC is 5V, R short;\u003cbr\u003e- VCC value of 12V, R 1K, more than 1\/8W resistor;\u003cbr\u003e- VCC value of 24V, R 2K, more than 1\/8W resistor;\u003cbr\u003e\u003cbr\u003eFunction selection (DIP switch on the drive panel)\u003cbr\u003e- Set the motor per revolution steps\u003cbr\u003eThe drive to set the number of steps per motor revolution is 200 (whole step), 400 (2 segments), 1600 (8 segments), 3200 steps (16 segments).\u003cbr\u003eThe user can drive the front panel DIP switch SW3 is SW4 bit of the drive to set the number of steps (such as Table 1):\u003cbr\u003eTable 1\u003cbr\u003e- Set the output phase current\u003cbr\u003e- To drive torque stepper motor, the user can drive panel DIP switch\u003cbr\u003e- SW1, SW2 is to set the drive output phase current (RMS) unit amperes, the switch position\u003cbr\u003e- Corresponding to the output current, output current value corresponding different types of drive. Concrete are shown in Table 2.\u003cbr\u003e- Output Current (A\u003cbr\u003eTable 2\u003cbr\u003eCurrent setting\u003cbr\u003e\u003cbr\u003e- the semi-flow functionality\u003cbr\u003e- The semi-flow function is a step pulse 200ms, the driver output current is automatically reduced to the rated output current50%, used to prevent motor heating.\u003cbr\u003eFourth, the power interface\u003cbr\u003e- 1, DC +, DC-: to connect the drive power\u003cbr\u003e- DC +: DC power level, power supply voltage DC 12 to 48V. The maximum current is 5A. The\u003cbr\u003eDC-: DC power supply negative level.\u003cbr\u003e2, A + A-B + B-: to connect the two-phase hybrid stepping motor\u003cbr\u003eDrive and two-phase hybrid stepper motor's connection with the four-wire system, the motor windings in parallel and series connection, and connection method, high-speed performance, but the drive current is large (for motor winding current of 1.73 times), Connected in series when the drive current is equal to the motor winding current.\u003cbr\u003eFive, the installation\u003cbr\u003e- Around to have 20mm of space, can not be placed next to the other heating equipment, to avoid dust, oil mist,\u003cbr\u003eCorrosive gases, high humidity is too big and strong vibration. +\u003cbr\u003eFigure 3.\u003cbr\u003eSix fault diagnosis\u003cbr\u003e1, the status light indicates\u003cbr\u003eRUN: green light in the normal work.\u003cbr\u003eERR: red light, power, light, power indicator\u003cbr\u003eSize: 10.5x8.5x3.3cm(approx)\u003c\/p\u003e\n\u003cimg src=\"https:\/\/ae01.alicdn.com\/kf\/He236654ff01e4461b3907273c5ea2dd0z.jpg\" class=\"detail-desc-decorate-image\"\u003e\u003cimg src=\"https:\/\/ae01.alicdn.com\/kf\/H77553a99bd4e46368cda2f21564c0af9p.jpg\" class=\"detail-desc-decorate-image\"\u003e\u003cimg src=\"https:\/\/ae01.alicdn.com\/kf\/Hc397f6a15fe8431bbcb8fe86468830fbk.jpg\" class=\"detail-desc-decorate-image\"\u003e\u003cimg src=\"https:\/\/ae01.alicdn.com\/kf\/Hc150b70a72af438d9ca4dea9bb464a43A.jpg\" class=\"detail-desc-decorate-image\"\u003e\u003cimg src=\"https:\/\/ae01.alicdn.com\/kf\/H2d60bfbea92d45ff9898a39239cf0c88d.jpg\" class=\"detail-desc-decorate-image\"\u003e\n\u003c\/div\u003e","published_at":"2020-02-19T21:25:58+08:00","created_at":"2020-02-19T21:41:01+08:00","vendor":"diymore","type":"Motor Speed Controller","tags":[],"price":1599,"price_min":1599,"price_max":1899,"available":true,"price_varies":true,"compare_at_price":null,"compare_at_price_min":0,"compare_at_price_max":0,"compare_at_price_varies":false,"variants":[{"id":31776718946375,"title":"5A-TB6600","option1":"5A-TB6600","option2":null,"option3":null,"sku":"010700","requires_shipping":true,"taxable":true,"featured_image":{"id":14509377224775,"product_id":4490370023495,"position":2,"created_at":"2020-05-06T01:56:08+08:00","updated_at":"2020-05-06T01:56:13+08:00","alt":"4A 5A Tb6600 Single Axis Stepper Motor Driver Controller Board Cnc Engraving Machine 1 Stepping","width":1000,"height":1000,"src":"\/\/www.diymore.cc\/cdn\/shop\/products\/He236654ff01e4461b3907273c5ea2dd0z_683.jpg?v=1588701373","variant_ids":[31776718946375]},"available":true,"name":"4A 5A TB6600 Single Axis Stepper Motor Driver Controller Board CNC Engraving Machine 1 Axis Stepping Motor Driver Module - 5A-TB6600","public_title":"5A-TB6600","options":["5A-TB6600"],"price":1899,"weight":0,"compare_at_price":null,"inventory_management":null,"barcode":"","featured_media":{"alt":"4A 5A Tb6600 Single Axis Stepper Motor Driver Controller Board Cnc Engraving Machine 1 Stepping","id":6682564100167,"position":2,"preview_image":{"aspect_ratio":1.0,"height":1000,"width":1000,"src":"\/\/www.diymore.cc\/cdn\/shop\/products\/He236654ff01e4461b3907273c5ea2dd0z_683.jpg?v=1588701373"}},"requires_selling_plan":false,"selling_plan_allocations":[]},{"id":31776718979143,"title":"4A-TB6600","option1":"4A-TB6600","option2":null,"option3":null,"sku":"010740","requires_shipping":true,"taxable":true,"featured_image":{"id":14509377650759,"product_id":4490370023495,"position":3,"created_at":"2020-05-06T01:56:12+08:00","updated_at":"2020-05-06T01:56:13+08:00","alt":"4A 5A Tb6600 Single Axis Stepper Motor Driver Controller Board Cnc Engraving Machine 1 Stepping","width":1000,"height":1000,"src":"\/\/www.diymore.cc\/cdn\/shop\/products\/Ha8b2526e84444ee9a78aea20742ee77e8_352.jpg?v=1588701373","variant_ids":[31776718979143]},"available":true,"name":"4A 5A TB6600 Single Axis Stepper Motor Driver Controller Board CNC Engraving Machine 1 Axis Stepping Motor Driver Module - 4A-TB6600","public_title":"4A-TB6600","options":["4A-TB6600"],"price":1599,"weight":0,"compare_at_price":null,"inventory_management":null,"barcode":"","featured_media":{"alt":"4A 5A Tb6600 Single Axis Stepper Motor Driver Controller Board Cnc Engraving Machine 1 Stepping","id":6682564427847,"position":3,"preview_image":{"aspect_ratio":1.0,"height":1000,"width":1000,"src":"\/\/www.diymore.cc\/cdn\/shop\/products\/Ha8b2526e84444ee9a78aea20742ee77e8_352.jpg?v=1588701373"}},"requires_selling_plan":false,"selling_plan_allocations":[]}],"images":["\/\/www.diymore.cc\/cdn\/shop\/products\/4A_5A_TB6600_Single_Axis_Stepper_Motor_Driver_Controller_Board_CNC_Engraving_Machine_1_Axis_Stepping_565.jpg?v=1588701373","\/\/www.diymore.cc\/cdn\/shop\/products\/He236654ff01e4461b3907273c5ea2dd0z_683.jpg?v=1588701373","\/\/www.diymore.cc\/cdn\/shop\/products\/Ha8b2526e84444ee9a78aea20742ee77e8_352.jpg?v=1588701373"],"featured_image":"\/\/www.diymore.cc\/cdn\/shop\/products\/4A_5A_TB6600_Single_Axis_Stepper_Motor_Driver_Controller_Board_CNC_Engraving_Machine_1_Axis_Stepping_565.jpg?v=1588701373","options":["Style"],"media":[{"alt":"4A 5A Tb6600 Single Axis Stepper Motor Driver Controller Board Cnc Engraving Machine 1 Stepping","id":6682563870791,"position":1,"preview_image":{"aspect_ratio":1.0,"height":1000,"width":1000,"src":"\/\/www.diymore.cc\/cdn\/shop\/products\/4A_5A_TB6600_Single_Axis_Stepper_Motor_Driver_Controller_Board_CNC_Engraving_Machine_1_Axis_Stepping_565.jpg?v=1588701373"},"aspect_ratio":1.0,"height":1000,"media_type":"image","src":"\/\/www.diymore.cc\/cdn\/shop\/products\/4A_5A_TB6600_Single_Axis_Stepper_Motor_Driver_Controller_Board_CNC_Engraving_Machine_1_Axis_Stepping_565.jpg?v=1588701373","width":1000},{"alt":"4A 5A Tb6600 Single Axis Stepper Motor Driver Controller Board Cnc Engraving Machine 1 Stepping","id":6682564100167,"position":2,"preview_image":{"aspect_ratio":1.0,"height":1000,"width":1000,"src":"\/\/www.diymore.cc\/cdn\/shop\/products\/He236654ff01e4461b3907273c5ea2dd0z_683.jpg?v=1588701373"},"aspect_ratio":1.0,"height":1000,"media_type":"image","src":"\/\/www.diymore.cc\/cdn\/shop\/products\/He236654ff01e4461b3907273c5ea2dd0z_683.jpg?v=1588701373","width":1000},{"alt":"4A 5A Tb6600 Single Axis Stepper Motor Driver Controller Board Cnc Engraving Machine 1 Stepping","id":6682564427847,"position":3,"preview_image":{"aspect_ratio":1.0,"height":1000,"width":1000,"src":"\/\/www.diymore.cc\/cdn\/shop\/products\/Ha8b2526e84444ee9a78aea20742ee77e8_352.jpg?v=1588701373"},"aspect_ratio":1.0,"height":1000,"media_type":"image","src":"\/\/www.diymore.cc\/cdn\/shop\/products\/Ha8b2526e84444ee9a78aea20742ee77e8_352.jpg?v=1588701373","width":1000}],"requires_selling_plan":false,"selling_plan_groups":[],"content":"\u003cdiv class=\"detailmodule_text-image\"\u003e\n\u003cp class=\"detail-desc-decorate-title\" data-spm-anchor-id=\"a2g0o.detail.1000023.i0.18421cf5ZdYzqP\"\u003e\u003cstrong\u003e4A-TB6600\u003c\/strong\u003e\u003cbr\u003e\u003cbr\u003eSpecifications:\u003cbr\u003eSupply Voltage: 9~42VDC\u003cbr\u003eMax Drive Current: 4A\u003cbr\u003eChopping Frequency: 20KHZ\u003cbr\u003e \u003cbr\u003eFeatures:\u003cbr\u003eBipolar constant current chopper\u003cbr\u003eHigh-speed optocoupler signal isolation input\u003cbr\u003eElectrical input signal is TTL compatible\u003cbr\u003eStationary current is automatically reduced by half\u003c\/p\u003e\n\u003cimg src=\"https:\/\/ae01.alicdn.com\/kf\/Ha8b2526e84444ee9a78aea20742ee77e8.jpg\" class=\"detail-desc-decorate-image\"\u003e\u003cimg src=\"https:\/\/ae01.alicdn.com\/kf\/H839a8652f0184ef1b95d3dcffecbbc93W.jpg\" class=\"detail-desc-decorate-image\"\u003e\u003cimg src=\"https:\/\/ae01.alicdn.com\/kf\/Hbc427740876349ef8df4d15bec752e8dA.jpg\" class=\"detail-desc-decorate-image\"\u003e\n\u003c\/div\u003e\n\u003cdiv class=\"detailmodule_text-image\"\u003e\n\u003cp class=\"detail-desc-decorate-title\"\u003e\u003cstrong\u003e5A-TB6600\u003c\/strong\u003e\u003cbr\u003e\u003cbr\u003eHY-DIV268N-5A subdivision-type two-phase hybrid stepping motor drive using DC 12 ~ 48V power supply, suitable for drive\u003cbr\u003eTwo-phase hybrid stepping motor dynamic voltage 12 to 48V, the current is less than 5A outer diameter of 35 to 86 mm. This drive using the drive's current loop subdivision control, the motor torque ripple is very small, low-speed running is very smooth, almost no vibration and noise. High-speed torque is much higher than other two-phase drive, high positioning accuracy. Widely used in the engraving machine, CNC machine tools, packaging machinery and other high resolution requirements on the device.\u003cbr\u003e\u003cbr\u003eThe main features\u003cbr\u003e- average current control, two-phase sinusoidal current drive output\u003cbr\u003e- DC 12 ~ 48V power supply, the internal integration of 12V and 5V regulator\u003cbr\u003e- optically isolated signal input \/ output\u003cbr\u003e- overvoltage, undervoltage, overcurrent, and white short-circuit protection\u003cbr\u003e\u003cbr\u003e- Input voltage DC 12 ~ 48V input\u003cbr\u003e- The input current of 1 to 5 amps, select the drive a stepper motor.\u003cbr\u003e- Output current of 0.2A ~ 5A\u003cbr\u003e- Temperature Operating Temperature -10 to 45 ℃; Storage temperature -40 ℃ to 70 ℃\u003cbr\u003e- Humidity not condensing, not drops\u003cbr\u003e- Gas prohibit combustible gas and conductive dust\u003cbr\u003e- Weight 200 grams\u003cbr\u003e\u003cbr\u003eControl signal interface\u003cbr\u003e- Figure 1 is a wiring schematic of the drive\u003cbr\u003e- 1, the definition of control signals\u003cbr\u003ePUL +: step pulse signal is input side or the positive pulse signal input positive terminal\u003cbr\u003ePUL-: the negative input of the negative input pulse signal or a positive pulse signal\u003cbr\u003eDIR +: stepping direction signal input to the positive terminal or negative pulse signal input to the positive terminal\u003cbr\u003eDIR -: stepping direction signal input of the negative side or reverse step pulse signal input negative terminal\u003cbr\u003eEN +: offline can reset signal input side is\u003cbr\u003eEN-: offline can reset signal input negative terminal\u003cbr\u003eOffline enable signal is active, reset drive failure to prohibit any pulse, the output of the drive\u003cbr\u003ePower component is turned off, the motor holding torque.\u003cbr\u003e- Control signal connections\u003cbr\u003e- PC control signal can be high, also can be low effective. When active high, the control signal\u003cbr\u003e- The negative side together as a signal to active low, positive side of all control signals together as a signal common.\u003cbr\u003e- For example, open-collector and PNP output interface circuit diagram is as follows:\u003cbr\u003eFigure 2. Input interface circuit (common cathode connection)\u003cbr\u003e- Note: the VCC is 5V, R short;\u003cbr\u003e- VCC value of 12V, R 1K, more than 1\/8W resistor;\u003cbr\u003e- VCC value of 24V, R 2K, more than 1\/8W resistor;\u003cbr\u003e\u003cbr\u003eFunction selection (DIP switch on the drive panel)\u003cbr\u003e- Set the motor per revolution steps\u003cbr\u003eThe drive to set the number of steps per motor revolution is 200 (whole step), 400 (2 segments), 1600 (8 segments), 3200 steps (16 segments).\u003cbr\u003eThe user can drive the front panel DIP switch SW3 is SW4 bit of the drive to set the number of steps (such as Table 1):\u003cbr\u003eTable 1\u003cbr\u003e- Set the output phase current\u003cbr\u003e- To drive torque stepper motor, the user can drive panel DIP switch\u003cbr\u003e- SW1, SW2 is to set the drive output phase current (RMS) unit amperes, the switch position\u003cbr\u003e- Corresponding to the output current, output current value corresponding different types of drive. Concrete are shown in Table 2.\u003cbr\u003e- Output Current (A\u003cbr\u003eTable 2\u003cbr\u003eCurrent setting\u003cbr\u003e\u003cbr\u003e- the semi-flow functionality\u003cbr\u003e- The semi-flow function is a step pulse 200ms, the driver output current is automatically reduced to the rated output current50%, used to prevent motor heating.\u003cbr\u003eFourth, the power interface\u003cbr\u003e- 1, DC +, DC-: to connect the drive power\u003cbr\u003e- DC +: DC power level, power supply voltage DC 12 to 48V. The maximum current is 5A. The\u003cbr\u003eDC-: DC power supply negative level.\u003cbr\u003e2, A + A-B + B-: to connect the two-phase hybrid stepping motor\u003cbr\u003eDrive and two-phase hybrid stepper motor's connection with the four-wire system, the motor windings in parallel and series connection, and connection method, high-speed performance, but the drive current is large (for motor winding current of 1.73 times), Connected in series when the drive current is equal to the motor winding current.\u003cbr\u003eFive, the installation\u003cbr\u003e- Around to have 20mm of space, can not be placed next to the other heating equipment, to avoid dust, oil mist,\u003cbr\u003eCorrosive gases, high humidity is too big and strong vibration. +\u003cbr\u003eFigure 3.\u003cbr\u003eSix fault diagnosis\u003cbr\u003e1, the status light indicates\u003cbr\u003eRUN: green light in the normal work.\u003cbr\u003eERR: red light, power, light, power indicator\u003cbr\u003eSize: 10.5x8.5x3.3cm(approx)\u003c\/p\u003e\n\u003cimg src=\"https:\/\/ae01.alicdn.com\/kf\/He236654ff01e4461b3907273c5ea2dd0z.jpg\" class=\"detail-desc-decorate-image\"\u003e\u003cimg src=\"https:\/\/ae01.alicdn.com\/kf\/H77553a99bd4e46368cda2f21564c0af9p.jpg\" class=\"detail-desc-decorate-image\"\u003e\u003cimg src=\"https:\/\/ae01.alicdn.com\/kf\/Hc397f6a15fe8431bbcb8fe86468830fbk.jpg\" class=\"detail-desc-decorate-image\"\u003e\u003cimg src=\"https:\/\/ae01.alicdn.com\/kf\/Hc150b70a72af438d9ca4dea9bb464a43A.jpg\" class=\"detail-desc-decorate-image\"\u003e\u003cimg src=\"https:\/\/ae01.alicdn.com\/kf\/H2d60bfbea92d45ff9898a39239cf0c88d.jpg\" class=\"detail-desc-decorate-image\"\u003e\n\u003c\/div\u003e"}
-
$7.99 USD{"id":4490370023495,"title":"4A 5A TB6600 Single Axis Stepper Motor Driver Controller Board CNC Engraving Machine 1 Axis Stepping Motor Driver Module","handle":"4a-5a-tb6600-single-axis-stepper-motor-driver-controller-board-cnc-engraving-machine-1-axis-stepping-motor-driver-module","description":"\u003cdiv class=\"detailmodule_text-image\"\u003e\n\u003cp class=\"detail-desc-decorate-title\" data-spm-anchor-id=\"a2g0o.detail.1000023.i0.18421cf5ZdYzqP\"\u003e\u003cstrong\u003e4A-TB6600\u003c\/strong\u003e\u003cbr\u003e\u003cbr\u003eSpecifications:\u003cbr\u003eSupply Voltage: 9~42VDC\u003cbr\u003eMax Drive Current: 4A\u003cbr\u003eChopping Frequency: 20KHZ\u003cbr\u003e \u003cbr\u003eFeatures:\u003cbr\u003eBipolar constant current chopper\u003cbr\u003eHigh-speed optocoupler signal isolation input\u003cbr\u003eElectrical input signal is TTL compatible\u003cbr\u003eStationary current is automatically reduced by half\u003c\/p\u003e\n\u003cimg src=\"https:\/\/ae01.alicdn.com\/kf\/Ha8b2526e84444ee9a78aea20742ee77e8.jpg\" class=\"detail-desc-decorate-image\"\u003e\u003cimg src=\"https:\/\/ae01.alicdn.com\/kf\/H839a8652f0184ef1b95d3dcffecbbc93W.jpg\" class=\"detail-desc-decorate-image\"\u003e\u003cimg src=\"https:\/\/ae01.alicdn.com\/kf\/Hbc427740876349ef8df4d15bec752e8dA.jpg\" class=\"detail-desc-decorate-image\"\u003e\n\u003c\/div\u003e\n\u003cdiv class=\"detailmodule_text-image\"\u003e\n\u003cp class=\"detail-desc-decorate-title\"\u003e\u003cstrong\u003e5A-TB6600\u003c\/strong\u003e\u003cbr\u003e\u003cbr\u003eHY-DIV268N-5A subdivision-type two-phase hybrid stepping motor drive using DC 12 ~ 48V power supply, suitable for drive\u003cbr\u003eTwo-phase hybrid stepping motor dynamic voltage 12 to 48V, the current is less than 5A outer diameter of 35 to 86 mm. This drive using the drive's current loop subdivision control, the motor torque ripple is very small, low-speed running is very smooth, almost no vibration and noise. High-speed torque is much higher than other two-phase drive, high positioning accuracy. Widely used in the engraving machine, CNC machine tools, packaging machinery and other high resolution requirements on the device.\u003cbr\u003e\u003cbr\u003eThe main features\u003cbr\u003e- average current control, two-phase sinusoidal current drive output\u003cbr\u003e- DC 12 ~ 48V power supply, the internal integration of 12V and 5V regulator\u003cbr\u003e- optically isolated signal input \/ output\u003cbr\u003e- overvoltage, undervoltage, overcurrent, and white short-circuit protection\u003cbr\u003e\u003cbr\u003e- Input voltage DC 12 ~ 48V input\u003cbr\u003e- The input current of 1 to 5 amps, select the drive a stepper motor.\u003cbr\u003e- Output current of 0.2A ~ 5A\u003cbr\u003e- Temperature Operating Temperature -10 to 45 ℃; Storage temperature -40 ℃ to 70 ℃\u003cbr\u003e- Humidity not condensing, not drops\u003cbr\u003e- Gas prohibit combustible gas and conductive dust\u003cbr\u003e- Weight 200 grams\u003cbr\u003e\u003cbr\u003eControl signal interface\u003cbr\u003e- Figure 1 is a wiring schematic of the drive\u003cbr\u003e- 1, the definition of control signals\u003cbr\u003ePUL +: step pulse signal is input side or the positive pulse signal input positive terminal\u003cbr\u003ePUL-: the negative input of the negative input pulse signal or a positive pulse signal\u003cbr\u003eDIR +: stepping direction signal input to the positive terminal or negative pulse signal input to the positive terminal\u003cbr\u003eDIR -: stepping direction signal input of the negative side or reverse step pulse signal input negative terminal\u003cbr\u003eEN +: offline can reset signal input side is\u003cbr\u003eEN-: offline can reset signal input negative terminal\u003cbr\u003eOffline enable signal is active, reset drive failure to prohibit any pulse, the output of the drive\u003cbr\u003ePower component is turned off, the motor holding torque.\u003cbr\u003e- Control signal connections\u003cbr\u003e- PC control signal can be high, also can be low effective. When active high, the control signal\u003cbr\u003e- The negative side together as a signal to active low, positive side of all control signals together as a signal common.\u003cbr\u003e- For example, open-collector and PNP output interface circuit diagram is as follows:\u003cbr\u003eFigure 2. Input interface circuit (common cathode connection)\u003cbr\u003e- Note: the VCC is 5V, R short;\u003cbr\u003e- VCC value of 12V, R 1K, more than 1\/8W resistor;\u003cbr\u003e- VCC value of 24V, R 2K, more than 1\/8W resistor;\u003cbr\u003e\u003cbr\u003eFunction selection (DIP switch on the drive panel)\u003cbr\u003e- Set the motor per revolution steps\u003cbr\u003eThe drive to set the number of steps per motor revolution is 200 (whole step), 400 (2 segments), 1600 (8 segments), 3200 steps (16 segments).\u003cbr\u003eThe user can drive the front panel DIP switch SW3 is SW4 bit of the drive to set the number of steps (such as Table 1):\u003cbr\u003eTable 1\u003cbr\u003e- Set the output phase current\u003cbr\u003e- To drive torque stepper motor, the user can drive panel DIP switch\u003cbr\u003e- SW1, SW2 is to set the drive output phase current (RMS) unit amperes, the switch position\u003cbr\u003e- Corresponding to the output current, output current value corresponding different types of drive. Concrete are shown in Table 2.\u003cbr\u003e- Output Current (A\u003cbr\u003eTable 2\u003cbr\u003eCurrent setting\u003cbr\u003e\u003cbr\u003e- the semi-flow functionality\u003cbr\u003e- The semi-flow function is a step pulse 200ms, the driver output current is automatically reduced to the rated output current50%, used to prevent motor heating.\u003cbr\u003eFourth, the power interface\u003cbr\u003e- 1, DC +, DC-: to connect the drive power\u003cbr\u003e- DC +: DC power level, power supply voltage DC 12 to 48V. The maximum current is 5A. The\u003cbr\u003eDC-: DC power supply negative level.\u003cbr\u003e2, A + A-B + B-: to connect the two-phase hybrid stepping motor\u003cbr\u003eDrive and two-phase hybrid stepper motor's connection with the four-wire system, the motor windings in parallel and series connection, and connection method, high-speed performance, but the drive current is large (for motor winding current of 1.73 times), Connected in series when the drive current is equal to the motor winding current.\u003cbr\u003eFive, the installation\u003cbr\u003e- Around to have 20mm of space, can not be placed next to the other heating equipment, to avoid dust, oil mist,\u003cbr\u003eCorrosive gases, high humidity is too big and strong vibration. +\u003cbr\u003eFigure 3.\u003cbr\u003eSix fault diagnosis\u003cbr\u003e1, the status light indicates\u003cbr\u003eRUN: green light in the normal work.\u003cbr\u003eERR: red light, power, light, power indicator\u003cbr\u003eSize: 10.5x8.5x3.3cm(approx)\u003c\/p\u003e\n\u003cimg src=\"https:\/\/ae01.alicdn.com\/kf\/He236654ff01e4461b3907273c5ea2dd0z.jpg\" class=\"detail-desc-decorate-image\"\u003e\u003cimg src=\"https:\/\/ae01.alicdn.com\/kf\/H77553a99bd4e46368cda2f21564c0af9p.jpg\" class=\"detail-desc-decorate-image\"\u003e\u003cimg src=\"https:\/\/ae01.alicdn.com\/kf\/Hc397f6a15fe8431bbcb8fe86468830fbk.jpg\" class=\"detail-desc-decorate-image\"\u003e\u003cimg src=\"https:\/\/ae01.alicdn.com\/kf\/Hc150b70a72af438d9ca4dea9bb464a43A.jpg\" class=\"detail-desc-decorate-image\"\u003e\u003cimg src=\"https:\/\/ae01.alicdn.com\/kf\/H2d60bfbea92d45ff9898a39239cf0c88d.jpg\" class=\"detail-desc-decorate-image\"\u003e\n\u003c\/div\u003e","published_at":"2020-02-19T21:25:58+08:00","created_at":"2020-02-19T21:41:01+08:00","vendor":"diymore","type":"Motor Speed Controller","tags":[],"price":1599,"price_min":1599,"price_max":1899,"available":true,"price_varies":true,"compare_at_price":null,"compare_at_price_min":0,"compare_at_price_max":0,"compare_at_price_varies":false,"variants":[{"id":31776718946375,"title":"5A-TB6600","option1":"5A-TB6600","option2":null,"option3":null,"sku":"010700","requires_shipping":true,"taxable":true,"featured_image":{"id":14509377224775,"product_id":4490370023495,"position":2,"created_at":"2020-05-06T01:56:08+08:00","updated_at":"2020-05-06T01:56:13+08:00","alt":"4A 5A Tb6600 Single Axis Stepper Motor Driver Controller Board Cnc Engraving Machine 1 Stepping","width":1000,"height":1000,"src":"\/\/www.diymore.cc\/cdn\/shop\/products\/He236654ff01e4461b3907273c5ea2dd0z_683.jpg?v=1588701373","variant_ids":[31776718946375]},"available":true,"name":"4A 5A TB6600 Single Axis Stepper Motor Driver Controller Board CNC Engraving Machine 1 Axis Stepping Motor Driver Module - 5A-TB6600","public_title":"5A-TB6600","options":["5A-TB6600"],"price":1899,"weight":0,"compare_at_price":null,"inventory_management":null,"barcode":"","featured_media":{"alt":"4A 5A Tb6600 Single Axis Stepper Motor Driver Controller Board Cnc Engraving Machine 1 Stepping","id":6682564100167,"position":2,"preview_image":{"aspect_ratio":1.0,"height":1000,"width":1000,"src":"\/\/www.diymore.cc\/cdn\/shop\/products\/He236654ff01e4461b3907273c5ea2dd0z_683.jpg?v=1588701373"}},"requires_selling_plan":false,"selling_plan_allocations":[]},{"id":31776718979143,"title":"4A-TB6600","option1":"4A-TB6600","option2":null,"option3":null,"sku":"010740","requires_shipping":true,"taxable":true,"featured_image":{"id":14509377650759,"product_id":4490370023495,"position":3,"created_at":"2020-05-06T01:56:12+08:00","updated_at":"2020-05-06T01:56:13+08:00","alt":"4A 5A Tb6600 Single Axis Stepper Motor Driver Controller Board Cnc Engraving Machine 1 Stepping","width":1000,"height":1000,"src":"\/\/www.diymore.cc\/cdn\/shop\/products\/Ha8b2526e84444ee9a78aea20742ee77e8_352.jpg?v=1588701373","variant_ids":[31776718979143]},"available":true,"name":"4A 5A TB6600 Single Axis Stepper Motor Driver Controller Board CNC Engraving Machine 1 Axis Stepping Motor Driver Module - 4A-TB6600","public_title":"4A-TB6600","options":["4A-TB6600"],"price":1599,"weight":0,"compare_at_price":null,"inventory_management":null,"barcode":"","featured_media":{"alt":"4A 5A Tb6600 Single Axis Stepper Motor Driver Controller Board Cnc Engraving Machine 1 Stepping","id":6682564427847,"position":3,"preview_image":{"aspect_ratio":1.0,"height":1000,"width":1000,"src":"\/\/www.diymore.cc\/cdn\/shop\/products\/Ha8b2526e84444ee9a78aea20742ee77e8_352.jpg?v=1588701373"}},"requires_selling_plan":false,"selling_plan_allocations":[]}],"images":["\/\/www.diymore.cc\/cdn\/shop\/products\/4A_5A_TB6600_Single_Axis_Stepper_Motor_Driver_Controller_Board_CNC_Engraving_Machine_1_Axis_Stepping_565.jpg?v=1588701373","\/\/www.diymore.cc\/cdn\/shop\/products\/He236654ff01e4461b3907273c5ea2dd0z_683.jpg?v=1588701373","\/\/www.diymore.cc\/cdn\/shop\/products\/Ha8b2526e84444ee9a78aea20742ee77e8_352.jpg?v=1588701373"],"featured_image":"\/\/www.diymore.cc\/cdn\/shop\/products\/4A_5A_TB6600_Single_Axis_Stepper_Motor_Driver_Controller_Board_CNC_Engraving_Machine_1_Axis_Stepping_565.jpg?v=1588701373","options":["Style"],"media":[{"alt":"4A 5A Tb6600 Single Axis Stepper Motor Driver Controller Board Cnc Engraving Machine 1 Stepping","id":6682563870791,"position":1,"preview_image":{"aspect_ratio":1.0,"height":1000,"width":1000,"src":"\/\/www.diymore.cc\/cdn\/shop\/products\/4A_5A_TB6600_Single_Axis_Stepper_Motor_Driver_Controller_Board_CNC_Engraving_Machine_1_Axis_Stepping_565.jpg?v=1588701373"},"aspect_ratio":1.0,"height":1000,"media_type":"image","src":"\/\/www.diymore.cc\/cdn\/shop\/products\/4A_5A_TB6600_Single_Axis_Stepper_Motor_Driver_Controller_Board_CNC_Engraving_Machine_1_Axis_Stepping_565.jpg?v=1588701373","width":1000},{"alt":"4A 5A Tb6600 Single Axis Stepper Motor Driver Controller Board Cnc Engraving Machine 1 Stepping","id":6682564100167,"position":2,"preview_image":{"aspect_ratio":1.0,"height":1000,"width":1000,"src":"\/\/www.diymore.cc\/cdn\/shop\/products\/He236654ff01e4461b3907273c5ea2dd0z_683.jpg?v=1588701373"},"aspect_ratio":1.0,"height":1000,"media_type":"image","src":"\/\/www.diymore.cc\/cdn\/shop\/products\/He236654ff01e4461b3907273c5ea2dd0z_683.jpg?v=1588701373","width":1000},{"alt":"4A 5A Tb6600 Single Axis Stepper Motor Driver Controller Board Cnc Engraving Machine 1 Stepping","id":6682564427847,"position":3,"preview_image":{"aspect_ratio":1.0,"height":1000,"width":1000,"src":"\/\/www.diymore.cc\/cdn\/shop\/products\/Ha8b2526e84444ee9a78aea20742ee77e8_352.jpg?v=1588701373"},"aspect_ratio":1.0,"height":1000,"media_type":"image","src":"\/\/www.diymore.cc\/cdn\/shop\/products\/Ha8b2526e84444ee9a78aea20742ee77e8_352.jpg?v=1588701373","width":1000}],"requires_selling_plan":false,"selling_plan_groups":[],"content":"\u003cdiv class=\"detailmodule_text-image\"\u003e\n\u003cp class=\"detail-desc-decorate-title\" data-spm-anchor-id=\"a2g0o.detail.1000023.i0.18421cf5ZdYzqP\"\u003e\u003cstrong\u003e4A-TB6600\u003c\/strong\u003e\u003cbr\u003e\u003cbr\u003eSpecifications:\u003cbr\u003eSupply Voltage: 9~42VDC\u003cbr\u003eMax Drive Current: 4A\u003cbr\u003eChopping Frequency: 20KHZ\u003cbr\u003e \u003cbr\u003eFeatures:\u003cbr\u003eBipolar constant current chopper\u003cbr\u003eHigh-speed optocoupler signal isolation input\u003cbr\u003eElectrical input signal is TTL compatible\u003cbr\u003eStationary current is automatically reduced by half\u003c\/p\u003e\n\u003cimg src=\"https:\/\/ae01.alicdn.com\/kf\/Ha8b2526e84444ee9a78aea20742ee77e8.jpg\" class=\"detail-desc-decorate-image\"\u003e\u003cimg src=\"https:\/\/ae01.alicdn.com\/kf\/H839a8652f0184ef1b95d3dcffecbbc93W.jpg\" class=\"detail-desc-decorate-image\"\u003e\u003cimg src=\"https:\/\/ae01.alicdn.com\/kf\/Hbc427740876349ef8df4d15bec752e8dA.jpg\" class=\"detail-desc-decorate-image\"\u003e\n\u003c\/div\u003e\n\u003cdiv class=\"detailmodule_text-image\"\u003e\n\u003cp class=\"detail-desc-decorate-title\"\u003e\u003cstrong\u003e5A-TB6600\u003c\/strong\u003e\u003cbr\u003e\u003cbr\u003eHY-DIV268N-5A subdivision-type two-phase hybrid stepping motor drive using DC 12 ~ 48V power supply, suitable for drive\u003cbr\u003eTwo-phase hybrid stepping motor dynamic voltage 12 to 48V, the current is less than 5A outer diameter of 35 to 86 mm. This drive using the drive's current loop subdivision control, the motor torque ripple is very small, low-speed running is very smooth, almost no vibration and noise. High-speed torque is much higher than other two-phase drive, high positioning accuracy. Widely used in the engraving machine, CNC machine tools, packaging machinery and other high resolution requirements on the device.\u003cbr\u003e\u003cbr\u003eThe main features\u003cbr\u003e- average current control, two-phase sinusoidal current drive output\u003cbr\u003e- DC 12 ~ 48V power supply, the internal integration of 12V and 5V regulator\u003cbr\u003e- optically isolated signal input \/ output\u003cbr\u003e- overvoltage, undervoltage, overcurrent, and white short-circuit protection\u003cbr\u003e\u003cbr\u003e- Input voltage DC 12 ~ 48V input\u003cbr\u003e- The input current of 1 to 5 amps, select the drive a stepper motor.\u003cbr\u003e- Output current of 0.2A ~ 5A\u003cbr\u003e- Temperature Operating Temperature -10 to 45 ℃; Storage temperature -40 ℃ to 70 ℃\u003cbr\u003e- Humidity not condensing, not drops\u003cbr\u003e- Gas prohibit combustible gas and conductive dust\u003cbr\u003e- Weight 200 grams\u003cbr\u003e\u003cbr\u003eControl signal interface\u003cbr\u003e- Figure 1 is a wiring schematic of the drive\u003cbr\u003e- 1, the definition of control signals\u003cbr\u003ePUL +: step pulse signal is input side or the positive pulse signal input positive terminal\u003cbr\u003ePUL-: the negative input of the negative input pulse signal or a positive pulse signal\u003cbr\u003eDIR +: stepping direction signal input to the positive terminal or negative pulse signal input to the positive terminal\u003cbr\u003eDIR -: stepping direction signal input of the negative side or reverse step pulse signal input negative terminal\u003cbr\u003eEN +: offline can reset signal input side is\u003cbr\u003eEN-: offline can reset signal input negative terminal\u003cbr\u003eOffline enable signal is active, reset drive failure to prohibit any pulse, the output of the drive\u003cbr\u003ePower component is turned off, the motor holding torque.\u003cbr\u003e- Control signal connections\u003cbr\u003e- PC control signal can be high, also can be low effective. When active high, the control signal\u003cbr\u003e- The negative side together as a signal to active low, positive side of all control signals together as a signal common.\u003cbr\u003e- For example, open-collector and PNP output interface circuit diagram is as follows:\u003cbr\u003eFigure 2. Input interface circuit (common cathode connection)\u003cbr\u003e- Note: the VCC is 5V, R short;\u003cbr\u003e- VCC value of 12V, R 1K, more than 1\/8W resistor;\u003cbr\u003e- VCC value of 24V, R 2K, more than 1\/8W resistor;\u003cbr\u003e\u003cbr\u003eFunction selection (DIP switch on the drive panel)\u003cbr\u003e- Set the motor per revolution steps\u003cbr\u003eThe drive to set the number of steps per motor revolution is 200 (whole step), 400 (2 segments), 1600 (8 segments), 3200 steps (16 segments).\u003cbr\u003eThe user can drive the front panel DIP switch SW3 is SW4 bit of the drive to set the number of steps (such as Table 1):\u003cbr\u003eTable 1\u003cbr\u003e- Set the output phase current\u003cbr\u003e- To drive torque stepper motor, the user can drive panel DIP switch\u003cbr\u003e- SW1, SW2 is to set the drive output phase current (RMS) unit amperes, the switch position\u003cbr\u003e- Corresponding to the output current, output current value corresponding different types of drive. Concrete are shown in Table 2.\u003cbr\u003e- Output Current (A\u003cbr\u003eTable 2\u003cbr\u003eCurrent setting\u003cbr\u003e\u003cbr\u003e- the semi-flow functionality\u003cbr\u003e- The semi-flow function is a step pulse 200ms, the driver output current is automatically reduced to the rated output current50%, used to prevent motor heating.\u003cbr\u003eFourth, the power interface\u003cbr\u003e- 1, DC +, DC-: to connect the drive power\u003cbr\u003e- DC +: DC power level, power supply voltage DC 12 to 48V. The maximum current is 5A. The\u003cbr\u003eDC-: DC power supply negative level.\u003cbr\u003e2, A + A-B + B-: to connect the two-phase hybrid stepping motor\u003cbr\u003eDrive and two-phase hybrid stepper motor's connection with the four-wire system, the motor windings in parallel and series connection, and connection method, high-speed performance, but the drive current is large (for motor winding current of 1.73 times), Connected in series when the drive current is equal to the motor winding current.\u003cbr\u003eFive, the installation\u003cbr\u003e- Around to have 20mm of space, can not be placed next to the other heating equipment, to avoid dust, oil mist,\u003cbr\u003eCorrosive gases, high humidity is too big and strong vibration. +\u003cbr\u003eFigure 3.\u003cbr\u003eSix fault diagnosis\u003cbr\u003e1, the status light indicates\u003cbr\u003eRUN: green light in the normal work.\u003cbr\u003eERR: red light, power, light, power indicator\u003cbr\u003eSize: 10.5x8.5x3.3cm(approx)\u003c\/p\u003e\n\u003cimg src=\"https:\/\/ae01.alicdn.com\/kf\/He236654ff01e4461b3907273c5ea2dd0z.jpg\" class=\"detail-desc-decorate-image\"\u003e\u003cimg src=\"https:\/\/ae01.alicdn.com\/kf\/H77553a99bd4e46368cda2f21564c0af9p.jpg\" class=\"detail-desc-decorate-image\"\u003e\u003cimg src=\"https:\/\/ae01.alicdn.com\/kf\/Hc397f6a15fe8431bbcb8fe86468830fbk.jpg\" class=\"detail-desc-decorate-image\"\u003e\u003cimg src=\"https:\/\/ae01.alicdn.com\/kf\/Hc150b70a72af438d9ca4dea9bb464a43A.jpg\" class=\"detail-desc-decorate-image\"\u003e\u003cimg src=\"https:\/\/ae01.alicdn.com\/kf\/H2d60bfbea92d45ff9898a39239cf0c88d.jpg\" class=\"detail-desc-decorate-image\"\u003e\n\u003c\/div\u003e"}
-
$8.99 USD{"id":4490370023495,"title":"4A 5A TB6600 Single Axis Stepper Motor Driver Controller Board CNC Engraving Machine 1 Axis Stepping Motor Driver Module","handle":"4a-5a-tb6600-single-axis-stepper-motor-driver-controller-board-cnc-engraving-machine-1-axis-stepping-motor-driver-module","description":"\u003cdiv class=\"detailmodule_text-image\"\u003e\n\u003cp class=\"detail-desc-decorate-title\" data-spm-anchor-id=\"a2g0o.detail.1000023.i0.18421cf5ZdYzqP\"\u003e\u003cstrong\u003e4A-TB6600\u003c\/strong\u003e\u003cbr\u003e\u003cbr\u003eSpecifications:\u003cbr\u003eSupply Voltage: 9~42VDC\u003cbr\u003eMax Drive Current: 4A\u003cbr\u003eChopping Frequency: 20KHZ\u003cbr\u003e \u003cbr\u003eFeatures:\u003cbr\u003eBipolar constant current chopper\u003cbr\u003eHigh-speed optocoupler signal isolation input\u003cbr\u003eElectrical input signal is TTL compatible\u003cbr\u003eStationary current is automatically reduced by half\u003c\/p\u003e\n\u003cimg src=\"https:\/\/ae01.alicdn.com\/kf\/Ha8b2526e84444ee9a78aea20742ee77e8.jpg\" class=\"detail-desc-decorate-image\"\u003e\u003cimg src=\"https:\/\/ae01.alicdn.com\/kf\/H839a8652f0184ef1b95d3dcffecbbc93W.jpg\" class=\"detail-desc-decorate-image\"\u003e\u003cimg src=\"https:\/\/ae01.alicdn.com\/kf\/Hbc427740876349ef8df4d15bec752e8dA.jpg\" class=\"detail-desc-decorate-image\"\u003e\n\u003c\/div\u003e\n\u003cdiv class=\"detailmodule_text-image\"\u003e\n\u003cp class=\"detail-desc-decorate-title\"\u003e\u003cstrong\u003e5A-TB6600\u003c\/strong\u003e\u003cbr\u003e\u003cbr\u003eHY-DIV268N-5A subdivision-type two-phase hybrid stepping motor drive using DC 12 ~ 48V power supply, suitable for drive\u003cbr\u003eTwo-phase hybrid stepping motor dynamic voltage 12 to 48V, the current is less than 5A outer diameter of 35 to 86 mm. This drive using the drive's current loop subdivision control, the motor torque ripple is very small, low-speed running is very smooth, almost no vibration and noise. High-speed torque is much higher than other two-phase drive, high positioning accuracy. Widely used in the engraving machine, CNC machine tools, packaging machinery and other high resolution requirements on the device.\u003cbr\u003e\u003cbr\u003eThe main features\u003cbr\u003e- average current control, two-phase sinusoidal current drive output\u003cbr\u003e- DC 12 ~ 48V power supply, the internal integration of 12V and 5V regulator\u003cbr\u003e- optically isolated signal input \/ output\u003cbr\u003e- overvoltage, undervoltage, overcurrent, and white short-circuit protection\u003cbr\u003e\u003cbr\u003e- Input voltage DC 12 ~ 48V input\u003cbr\u003e- The input current of 1 to 5 amps, select the drive a stepper motor.\u003cbr\u003e- Output current of 0.2A ~ 5A\u003cbr\u003e- Temperature Operating Temperature -10 to 45 ℃; Storage temperature -40 ℃ to 70 ℃\u003cbr\u003e- Humidity not condensing, not drops\u003cbr\u003e- Gas prohibit combustible gas and conductive dust\u003cbr\u003e- Weight 200 grams\u003cbr\u003e\u003cbr\u003eControl signal interface\u003cbr\u003e- Figure 1 is a wiring schematic of the drive\u003cbr\u003e- 1, the definition of control signals\u003cbr\u003ePUL +: step pulse signal is input side or the positive pulse signal input positive terminal\u003cbr\u003ePUL-: the negative input of the negative input pulse signal or a positive pulse signal\u003cbr\u003eDIR +: stepping direction signal input to the positive terminal or negative pulse signal input to the positive terminal\u003cbr\u003eDIR -: stepping direction signal input of the negative side or reverse step pulse signal input negative terminal\u003cbr\u003eEN +: offline can reset signal input side is\u003cbr\u003eEN-: offline can reset signal input negative terminal\u003cbr\u003eOffline enable signal is active, reset drive failure to prohibit any pulse, the output of the drive\u003cbr\u003ePower component is turned off, the motor holding torque.\u003cbr\u003e- Control signal connections\u003cbr\u003e- PC control signal can be high, also can be low effective. When active high, the control signal\u003cbr\u003e- The negative side together as a signal to active low, positive side of all control signals together as a signal common.\u003cbr\u003e- For example, open-collector and PNP output interface circuit diagram is as follows:\u003cbr\u003eFigure 2. Input interface circuit (common cathode connection)\u003cbr\u003e- Note: the VCC is 5V, R short;\u003cbr\u003e- VCC value of 12V, R 1K, more than 1\/8W resistor;\u003cbr\u003e- VCC value of 24V, R 2K, more than 1\/8W resistor;\u003cbr\u003e\u003cbr\u003eFunction selection (DIP switch on the drive panel)\u003cbr\u003e- Set the motor per revolution steps\u003cbr\u003eThe drive to set the number of steps per motor revolution is 200 (whole step), 400 (2 segments), 1600 (8 segments), 3200 steps (16 segments).\u003cbr\u003eThe user can drive the front panel DIP switch SW3 is SW4 bit of the drive to set the number of steps (such as Table 1):\u003cbr\u003eTable 1\u003cbr\u003e- Set the output phase current\u003cbr\u003e- To drive torque stepper motor, the user can drive panel DIP switch\u003cbr\u003e- SW1, SW2 is to set the drive output phase current (RMS) unit amperes, the switch position\u003cbr\u003e- Corresponding to the output current, output current value corresponding different types of drive. Concrete are shown in Table 2.\u003cbr\u003e- Output Current (A\u003cbr\u003eTable 2\u003cbr\u003eCurrent setting\u003cbr\u003e\u003cbr\u003e- the semi-flow functionality\u003cbr\u003e- The semi-flow function is a step pulse 200ms, the driver output current is automatically reduced to the rated output current50%, used to prevent motor heating.\u003cbr\u003eFourth, the power interface\u003cbr\u003e- 1, DC +, DC-: to connect the drive power\u003cbr\u003e- DC +: DC power level, power supply voltage DC 12 to 48V. The maximum current is 5A. The\u003cbr\u003eDC-: DC power supply negative level.\u003cbr\u003e2, A + A-B + B-: to connect the two-phase hybrid stepping motor\u003cbr\u003eDrive and two-phase hybrid stepper motor's connection with the four-wire system, the motor windings in parallel and series connection, and connection method, high-speed performance, but the drive current is large (for motor winding current of 1.73 times), Connected in series when the drive current is equal to the motor winding current.\u003cbr\u003eFive, the installation\u003cbr\u003e- Around to have 20mm of space, can not be placed next to the other heating equipment, to avoid dust, oil mist,\u003cbr\u003eCorrosive gases, high humidity is too big and strong vibration. +\u003cbr\u003eFigure 3.\u003cbr\u003eSix fault diagnosis\u003cbr\u003e1, the status light indicates\u003cbr\u003eRUN: green light in the normal work.\u003cbr\u003eERR: red light, power, light, power indicator\u003cbr\u003eSize: 10.5x8.5x3.3cm(approx)\u003c\/p\u003e\n\u003cimg src=\"https:\/\/ae01.alicdn.com\/kf\/He236654ff01e4461b3907273c5ea2dd0z.jpg\" class=\"detail-desc-decorate-image\"\u003e\u003cimg src=\"https:\/\/ae01.alicdn.com\/kf\/H77553a99bd4e46368cda2f21564c0af9p.jpg\" class=\"detail-desc-decorate-image\"\u003e\u003cimg src=\"https:\/\/ae01.alicdn.com\/kf\/Hc397f6a15fe8431bbcb8fe86468830fbk.jpg\" class=\"detail-desc-decorate-image\"\u003e\u003cimg src=\"https:\/\/ae01.alicdn.com\/kf\/Hc150b70a72af438d9ca4dea9bb464a43A.jpg\" class=\"detail-desc-decorate-image\"\u003e\u003cimg src=\"https:\/\/ae01.alicdn.com\/kf\/H2d60bfbea92d45ff9898a39239cf0c88d.jpg\" class=\"detail-desc-decorate-image\"\u003e\n\u003c\/div\u003e","published_at":"2020-02-19T21:25:58+08:00","created_at":"2020-02-19T21:41:01+08:00","vendor":"diymore","type":"Motor Speed Controller","tags":[],"price":1599,"price_min":1599,"price_max":1899,"available":true,"price_varies":true,"compare_at_price":null,"compare_at_price_min":0,"compare_at_price_max":0,"compare_at_price_varies":false,"variants":[{"id":31776718946375,"title":"5A-TB6600","option1":"5A-TB6600","option2":null,"option3":null,"sku":"010700","requires_shipping":true,"taxable":true,"featured_image":{"id":14509377224775,"product_id":4490370023495,"position":2,"created_at":"2020-05-06T01:56:08+08:00","updated_at":"2020-05-06T01:56:13+08:00","alt":"4A 5A Tb6600 Single Axis Stepper Motor Driver Controller Board Cnc Engraving Machine 1 Stepping","width":1000,"height":1000,"src":"\/\/www.diymore.cc\/cdn\/shop\/products\/He236654ff01e4461b3907273c5ea2dd0z_683.jpg?v=1588701373","variant_ids":[31776718946375]},"available":true,"name":"4A 5A TB6600 Single Axis Stepper Motor Driver Controller Board CNC Engraving Machine 1 Axis Stepping Motor Driver Module - 5A-TB6600","public_title":"5A-TB6600","options":["5A-TB6600"],"price":1899,"weight":0,"compare_at_price":null,"inventory_management":null,"barcode":"","featured_media":{"alt":"4A 5A Tb6600 Single Axis Stepper Motor Driver Controller Board Cnc Engraving Machine 1 Stepping","id":6682564100167,"position":2,"preview_image":{"aspect_ratio":1.0,"height":1000,"width":1000,"src":"\/\/www.diymore.cc\/cdn\/shop\/products\/He236654ff01e4461b3907273c5ea2dd0z_683.jpg?v=1588701373"}},"requires_selling_plan":false,"selling_plan_allocations":[]},{"id":31776718979143,"title":"4A-TB6600","option1":"4A-TB6600","option2":null,"option3":null,"sku":"010740","requires_shipping":true,"taxable":true,"featured_image":{"id":14509377650759,"product_id":4490370023495,"position":3,"created_at":"2020-05-06T01:56:12+08:00","updated_at":"2020-05-06T01:56:13+08:00","alt":"4A 5A Tb6600 Single Axis Stepper Motor Driver Controller Board Cnc Engraving Machine 1 Stepping","width":1000,"height":1000,"src":"\/\/www.diymore.cc\/cdn\/shop\/products\/Ha8b2526e84444ee9a78aea20742ee77e8_352.jpg?v=1588701373","variant_ids":[31776718979143]},"available":true,"name":"4A 5A TB6600 Single Axis Stepper Motor Driver Controller Board CNC Engraving Machine 1 Axis Stepping Motor Driver Module - 4A-TB6600","public_title":"4A-TB6600","options":["4A-TB6600"],"price":1599,"weight":0,"compare_at_price":null,"inventory_management":null,"barcode":"","featured_media":{"alt":"4A 5A Tb6600 Single Axis Stepper Motor Driver Controller Board Cnc Engraving Machine 1 Stepping","id":6682564427847,"position":3,"preview_image":{"aspect_ratio":1.0,"height":1000,"width":1000,"src":"\/\/www.diymore.cc\/cdn\/shop\/products\/Ha8b2526e84444ee9a78aea20742ee77e8_352.jpg?v=1588701373"}},"requires_selling_plan":false,"selling_plan_allocations":[]}],"images":["\/\/www.diymore.cc\/cdn\/shop\/products\/4A_5A_TB6600_Single_Axis_Stepper_Motor_Driver_Controller_Board_CNC_Engraving_Machine_1_Axis_Stepping_565.jpg?v=1588701373","\/\/www.diymore.cc\/cdn\/shop\/products\/He236654ff01e4461b3907273c5ea2dd0z_683.jpg?v=1588701373","\/\/www.diymore.cc\/cdn\/shop\/products\/Ha8b2526e84444ee9a78aea20742ee77e8_352.jpg?v=1588701373"],"featured_image":"\/\/www.diymore.cc\/cdn\/shop\/products\/4A_5A_TB6600_Single_Axis_Stepper_Motor_Driver_Controller_Board_CNC_Engraving_Machine_1_Axis_Stepping_565.jpg?v=1588701373","options":["Style"],"media":[{"alt":"4A 5A Tb6600 Single Axis Stepper Motor Driver Controller Board Cnc Engraving Machine 1 Stepping","id":6682563870791,"position":1,"preview_image":{"aspect_ratio":1.0,"height":1000,"width":1000,"src":"\/\/www.diymore.cc\/cdn\/shop\/products\/4A_5A_TB6600_Single_Axis_Stepper_Motor_Driver_Controller_Board_CNC_Engraving_Machine_1_Axis_Stepping_565.jpg?v=1588701373"},"aspect_ratio":1.0,"height":1000,"media_type":"image","src":"\/\/www.diymore.cc\/cdn\/shop\/products\/4A_5A_TB6600_Single_Axis_Stepper_Motor_Driver_Controller_Board_CNC_Engraving_Machine_1_Axis_Stepping_565.jpg?v=1588701373","width":1000},{"alt":"4A 5A Tb6600 Single Axis Stepper Motor Driver Controller Board Cnc Engraving Machine 1 Stepping","id":6682564100167,"position":2,"preview_image":{"aspect_ratio":1.0,"height":1000,"width":1000,"src":"\/\/www.diymore.cc\/cdn\/shop\/products\/He236654ff01e4461b3907273c5ea2dd0z_683.jpg?v=1588701373"},"aspect_ratio":1.0,"height":1000,"media_type":"image","src":"\/\/www.diymore.cc\/cdn\/shop\/products\/He236654ff01e4461b3907273c5ea2dd0z_683.jpg?v=1588701373","width":1000},{"alt":"4A 5A Tb6600 Single Axis Stepper Motor Driver Controller Board Cnc Engraving Machine 1 Stepping","id":6682564427847,"position":3,"preview_image":{"aspect_ratio":1.0,"height":1000,"width":1000,"src":"\/\/www.diymore.cc\/cdn\/shop\/products\/Ha8b2526e84444ee9a78aea20742ee77e8_352.jpg?v=1588701373"},"aspect_ratio":1.0,"height":1000,"media_type":"image","src":"\/\/www.diymore.cc\/cdn\/shop\/products\/Ha8b2526e84444ee9a78aea20742ee77e8_352.jpg?v=1588701373","width":1000}],"requires_selling_plan":false,"selling_plan_groups":[],"content":"\u003cdiv class=\"detailmodule_text-image\"\u003e\n\u003cp class=\"detail-desc-decorate-title\" data-spm-anchor-id=\"a2g0o.detail.1000023.i0.18421cf5ZdYzqP\"\u003e\u003cstrong\u003e4A-TB6600\u003c\/strong\u003e\u003cbr\u003e\u003cbr\u003eSpecifications:\u003cbr\u003eSupply Voltage: 9~42VDC\u003cbr\u003eMax Drive Current: 4A\u003cbr\u003eChopping Frequency: 20KHZ\u003cbr\u003e \u003cbr\u003eFeatures:\u003cbr\u003eBipolar constant current chopper\u003cbr\u003eHigh-speed optocoupler signal isolation input\u003cbr\u003eElectrical input signal is TTL compatible\u003cbr\u003eStationary current is automatically reduced by half\u003c\/p\u003e\n\u003cimg src=\"https:\/\/ae01.alicdn.com\/kf\/Ha8b2526e84444ee9a78aea20742ee77e8.jpg\" class=\"detail-desc-decorate-image\"\u003e\u003cimg src=\"https:\/\/ae01.alicdn.com\/kf\/H839a8652f0184ef1b95d3dcffecbbc93W.jpg\" class=\"detail-desc-decorate-image\"\u003e\u003cimg src=\"https:\/\/ae01.alicdn.com\/kf\/Hbc427740876349ef8df4d15bec752e8dA.jpg\" class=\"detail-desc-decorate-image\"\u003e\n\u003c\/div\u003e\n\u003cdiv class=\"detailmodule_text-image\"\u003e\n\u003cp class=\"detail-desc-decorate-title\"\u003e\u003cstrong\u003e5A-TB6600\u003c\/strong\u003e\u003cbr\u003e\u003cbr\u003eHY-DIV268N-5A subdivision-type two-phase hybrid stepping motor drive using DC 12 ~ 48V power supply, suitable for drive\u003cbr\u003eTwo-phase hybrid stepping motor dynamic voltage 12 to 48V, the current is less than 5A outer diameter of 35 to 86 mm. This drive using the drive's current loop subdivision control, the motor torque ripple is very small, low-speed running is very smooth, almost no vibration and noise. High-speed torque is much higher than other two-phase drive, high positioning accuracy. Widely used in the engraving machine, CNC machine tools, packaging machinery and other high resolution requirements on the device.\u003cbr\u003e\u003cbr\u003eThe main features\u003cbr\u003e- average current control, two-phase sinusoidal current drive output\u003cbr\u003e- DC 12 ~ 48V power supply, the internal integration of 12V and 5V regulator\u003cbr\u003e- optically isolated signal input \/ output\u003cbr\u003e- overvoltage, undervoltage, overcurrent, and white short-circuit protection\u003cbr\u003e\u003cbr\u003e- Input voltage DC 12 ~ 48V input\u003cbr\u003e- The input current of 1 to 5 amps, select the drive a stepper motor.\u003cbr\u003e- Output current of 0.2A ~ 5A\u003cbr\u003e- Temperature Operating Temperature -10 to 45 ℃; Storage temperature -40 ℃ to 70 ℃\u003cbr\u003e- Humidity not condensing, not drops\u003cbr\u003e- Gas prohibit combustible gas and conductive dust\u003cbr\u003e- Weight 200 grams\u003cbr\u003e\u003cbr\u003eControl signal interface\u003cbr\u003e- Figure 1 is a wiring schematic of the drive\u003cbr\u003e- 1, the definition of control signals\u003cbr\u003ePUL +: step pulse signal is input side or the positive pulse signal input positive terminal\u003cbr\u003ePUL-: the negative input of the negative input pulse signal or a positive pulse signal\u003cbr\u003eDIR +: stepping direction signal input to the positive terminal or negative pulse signal input to the positive terminal\u003cbr\u003eDIR -: stepping direction signal input of the negative side or reverse step pulse signal input negative terminal\u003cbr\u003eEN +: offline can reset signal input side is\u003cbr\u003eEN-: offline can reset signal input negative terminal\u003cbr\u003eOffline enable signal is active, reset drive failure to prohibit any pulse, the output of the drive\u003cbr\u003ePower component is turned off, the motor holding torque.\u003cbr\u003e- Control signal connections\u003cbr\u003e- PC control signal can be high, also can be low effective. When active high, the control signal\u003cbr\u003e- The negative side together as a signal to active low, positive side of all control signals together as a signal common.\u003cbr\u003e- For example, open-collector and PNP output interface circuit diagram is as follows:\u003cbr\u003eFigure 2. Input interface circuit (common cathode connection)\u003cbr\u003e- Note: the VCC is 5V, R short;\u003cbr\u003e- VCC value of 12V, R 1K, more than 1\/8W resistor;\u003cbr\u003e- VCC value of 24V, R 2K, more than 1\/8W resistor;\u003cbr\u003e\u003cbr\u003eFunction selection (DIP switch on the drive panel)\u003cbr\u003e- Set the motor per revolution steps\u003cbr\u003eThe drive to set the number of steps per motor revolution is 200 (whole step), 400 (2 segments), 1600 (8 segments), 3200 steps (16 segments).\u003cbr\u003eThe user can drive the front panel DIP switch SW3 is SW4 bit of the drive to set the number of steps (such as Table 1):\u003cbr\u003eTable 1\u003cbr\u003e- Set the output phase current\u003cbr\u003e- To drive torque stepper motor, the user can drive panel DIP switch\u003cbr\u003e- SW1, SW2 is to set the drive output phase current (RMS) unit amperes, the switch position\u003cbr\u003e- Corresponding to the output current, output current value corresponding different types of drive. Concrete are shown in Table 2.\u003cbr\u003e- Output Current (A\u003cbr\u003eTable 2\u003cbr\u003eCurrent setting\u003cbr\u003e\u003cbr\u003e- the semi-flow functionality\u003cbr\u003e- The semi-flow function is a step pulse 200ms, the driver output current is automatically reduced to the rated output current50%, used to prevent motor heating.\u003cbr\u003eFourth, the power interface\u003cbr\u003e- 1, DC +, DC-: to connect the drive power\u003cbr\u003e- DC +: DC power level, power supply voltage DC 12 to 48V. The maximum current is 5A. The\u003cbr\u003eDC-: DC power supply negative level.\u003cbr\u003e2, A + A-B + B-: to connect the two-phase hybrid stepping motor\u003cbr\u003eDrive and two-phase hybrid stepper motor's connection with the four-wire system, the motor windings in parallel and series connection, and connection method, high-speed performance, but the drive current is large (for motor winding current of 1.73 times), Connected in series when the drive current is equal to the motor winding current.\u003cbr\u003eFive, the installation\u003cbr\u003e- Around to have 20mm of space, can not be placed next to the other heating equipment, to avoid dust, oil mist,\u003cbr\u003eCorrosive gases, high humidity is too big and strong vibration. +\u003cbr\u003eFigure 3.\u003cbr\u003eSix fault diagnosis\u003cbr\u003e1, the status light indicates\u003cbr\u003eRUN: green light in the normal work.\u003cbr\u003eERR: red light, power, light, power indicator\u003cbr\u003eSize: 10.5x8.5x3.3cm(approx)\u003c\/p\u003e\n\u003cimg src=\"https:\/\/ae01.alicdn.com\/kf\/He236654ff01e4461b3907273c5ea2dd0z.jpg\" class=\"detail-desc-decorate-image\"\u003e\u003cimg src=\"https:\/\/ae01.alicdn.com\/kf\/H77553a99bd4e46368cda2f21564c0af9p.jpg\" class=\"detail-desc-decorate-image\"\u003e\u003cimg src=\"https:\/\/ae01.alicdn.com\/kf\/Hc397f6a15fe8431bbcb8fe86468830fbk.jpg\" class=\"detail-desc-decorate-image\"\u003e\u003cimg src=\"https:\/\/ae01.alicdn.com\/kf\/Hc150b70a72af438d9ca4dea9bb464a43A.jpg\" class=\"detail-desc-decorate-image\"\u003e\u003cimg src=\"https:\/\/ae01.alicdn.com\/kf\/H2d60bfbea92d45ff9898a39239cf0c88d.jpg\" class=\"detail-desc-decorate-image\"\u003e\n\u003c\/div\u003e"}
-
$5.99 USD{"id":4490370023495,"title":"4A 5A TB6600 Single Axis Stepper Motor Driver Controller Board CNC Engraving Machine 1 Axis Stepping Motor Driver Module","handle":"4a-5a-tb6600-single-axis-stepper-motor-driver-controller-board-cnc-engraving-machine-1-axis-stepping-motor-driver-module","description":"\u003cdiv class=\"detailmodule_text-image\"\u003e\n\u003cp class=\"detail-desc-decorate-title\" data-spm-anchor-id=\"a2g0o.detail.1000023.i0.18421cf5ZdYzqP\"\u003e\u003cstrong\u003e4A-TB6600\u003c\/strong\u003e\u003cbr\u003e\u003cbr\u003eSpecifications:\u003cbr\u003eSupply Voltage: 9~42VDC\u003cbr\u003eMax Drive Current: 4A\u003cbr\u003eChopping Frequency: 20KHZ\u003cbr\u003e \u003cbr\u003eFeatures:\u003cbr\u003eBipolar constant current chopper\u003cbr\u003eHigh-speed optocoupler signal isolation input\u003cbr\u003eElectrical input signal is TTL compatible\u003cbr\u003eStationary current is automatically reduced by half\u003c\/p\u003e\n\u003cimg src=\"https:\/\/ae01.alicdn.com\/kf\/Ha8b2526e84444ee9a78aea20742ee77e8.jpg\" class=\"detail-desc-decorate-image\"\u003e\u003cimg src=\"https:\/\/ae01.alicdn.com\/kf\/H839a8652f0184ef1b95d3dcffecbbc93W.jpg\" class=\"detail-desc-decorate-image\"\u003e\u003cimg src=\"https:\/\/ae01.alicdn.com\/kf\/Hbc427740876349ef8df4d15bec752e8dA.jpg\" class=\"detail-desc-decorate-image\"\u003e\n\u003c\/div\u003e\n\u003cdiv class=\"detailmodule_text-image\"\u003e\n\u003cp class=\"detail-desc-decorate-title\"\u003e\u003cstrong\u003e5A-TB6600\u003c\/strong\u003e\u003cbr\u003e\u003cbr\u003eHY-DIV268N-5A subdivision-type two-phase hybrid stepping motor drive using DC 12 ~ 48V power supply, suitable for drive\u003cbr\u003eTwo-phase hybrid stepping motor dynamic voltage 12 to 48V, the current is less than 5A outer diameter of 35 to 86 mm. This drive using the drive's current loop subdivision control, the motor torque ripple is very small, low-speed running is very smooth, almost no vibration and noise. High-speed torque is much higher than other two-phase drive, high positioning accuracy. Widely used in the engraving machine, CNC machine tools, packaging machinery and other high resolution requirements on the device.\u003cbr\u003e\u003cbr\u003eThe main features\u003cbr\u003e- average current control, two-phase sinusoidal current drive output\u003cbr\u003e- DC 12 ~ 48V power supply, the internal integration of 12V and 5V regulator\u003cbr\u003e- optically isolated signal input \/ output\u003cbr\u003e- overvoltage, undervoltage, overcurrent, and white short-circuit protection\u003cbr\u003e\u003cbr\u003e- Input voltage DC 12 ~ 48V input\u003cbr\u003e- The input current of 1 to 5 amps, select the drive a stepper motor.\u003cbr\u003e- Output current of 0.2A ~ 5A\u003cbr\u003e- Temperature Operating Temperature -10 to 45 ℃; Storage temperature -40 ℃ to 70 ℃\u003cbr\u003e- Humidity not condensing, not drops\u003cbr\u003e- Gas prohibit combustible gas and conductive dust\u003cbr\u003e- Weight 200 grams\u003cbr\u003e\u003cbr\u003eControl signal interface\u003cbr\u003e- Figure 1 is a wiring schematic of the drive\u003cbr\u003e- 1, the definition of control signals\u003cbr\u003ePUL +: step pulse signal is input side or the positive pulse signal input positive terminal\u003cbr\u003ePUL-: the negative input of the negative input pulse signal or a positive pulse signal\u003cbr\u003eDIR +: stepping direction signal input to the positive terminal or negative pulse signal input to the positive terminal\u003cbr\u003eDIR -: stepping direction signal input of the negative side or reverse step pulse signal input negative terminal\u003cbr\u003eEN +: offline can reset signal input side is\u003cbr\u003eEN-: offline can reset signal input negative terminal\u003cbr\u003eOffline enable signal is active, reset drive failure to prohibit any pulse, the output of the drive\u003cbr\u003ePower component is turned off, the motor holding torque.\u003cbr\u003e- Control signal connections\u003cbr\u003e- PC control signal can be high, also can be low effective. When active high, the control signal\u003cbr\u003e- The negative side together as a signal to active low, positive side of all control signals together as a signal common.\u003cbr\u003e- For example, open-collector and PNP output interface circuit diagram is as follows:\u003cbr\u003eFigure 2. Input interface circuit (common cathode connection)\u003cbr\u003e- Note: the VCC is 5V, R short;\u003cbr\u003e- VCC value of 12V, R 1K, more than 1\/8W resistor;\u003cbr\u003e- VCC value of 24V, R 2K, more than 1\/8W resistor;\u003cbr\u003e\u003cbr\u003eFunction selection (DIP switch on the drive panel)\u003cbr\u003e- Set the motor per revolution steps\u003cbr\u003eThe drive to set the number of steps per motor revolution is 200 (whole step), 400 (2 segments), 1600 (8 segments), 3200 steps (16 segments).\u003cbr\u003eThe user can drive the front panel DIP switch SW3 is SW4 bit of the drive to set the number of steps (such as Table 1):\u003cbr\u003eTable 1\u003cbr\u003e- Set the output phase current\u003cbr\u003e- To drive torque stepper motor, the user can drive panel DIP switch\u003cbr\u003e- SW1, SW2 is to set the drive output phase current (RMS) unit amperes, the switch position\u003cbr\u003e- Corresponding to the output current, output current value corresponding different types of drive. Concrete are shown in Table 2.\u003cbr\u003e- Output Current (A\u003cbr\u003eTable 2\u003cbr\u003eCurrent setting\u003cbr\u003e\u003cbr\u003e- the semi-flow functionality\u003cbr\u003e- The semi-flow function is a step pulse 200ms, the driver output current is automatically reduced to the rated output current50%, used to prevent motor heating.\u003cbr\u003eFourth, the power interface\u003cbr\u003e- 1, DC +, DC-: to connect the drive power\u003cbr\u003e- DC +: DC power level, power supply voltage DC 12 to 48V. The maximum current is 5A. The\u003cbr\u003eDC-: DC power supply negative level.\u003cbr\u003e2, A + A-B + B-: to connect the two-phase hybrid stepping motor\u003cbr\u003eDrive and two-phase hybrid stepper motor's connection with the four-wire system, the motor windings in parallel and series connection, and connection method, high-speed performance, but the drive current is large (for motor winding current of 1.73 times), Connected in series when the drive current is equal to the motor winding current.\u003cbr\u003eFive, the installation\u003cbr\u003e- Around to have 20mm of space, can not be placed next to the other heating equipment, to avoid dust, oil mist,\u003cbr\u003eCorrosive gases, high humidity is too big and strong vibration. +\u003cbr\u003eFigure 3.\u003cbr\u003eSix fault diagnosis\u003cbr\u003e1, the status light indicates\u003cbr\u003eRUN: green light in the normal work.\u003cbr\u003eERR: red light, power, light, power indicator\u003cbr\u003eSize: 10.5x8.5x3.3cm(approx)\u003c\/p\u003e\n\u003cimg src=\"https:\/\/ae01.alicdn.com\/kf\/He236654ff01e4461b3907273c5ea2dd0z.jpg\" class=\"detail-desc-decorate-image\"\u003e\u003cimg src=\"https:\/\/ae01.alicdn.com\/kf\/H77553a99bd4e46368cda2f21564c0af9p.jpg\" class=\"detail-desc-decorate-image\"\u003e\u003cimg src=\"https:\/\/ae01.alicdn.com\/kf\/Hc397f6a15fe8431bbcb8fe86468830fbk.jpg\" class=\"detail-desc-decorate-image\"\u003e\u003cimg src=\"https:\/\/ae01.alicdn.com\/kf\/Hc150b70a72af438d9ca4dea9bb464a43A.jpg\" class=\"detail-desc-decorate-image\"\u003e\u003cimg src=\"https:\/\/ae01.alicdn.com\/kf\/H2d60bfbea92d45ff9898a39239cf0c88d.jpg\" class=\"detail-desc-decorate-image\"\u003e\n\u003c\/div\u003e","published_at":"2020-02-19T21:25:58+08:00","created_at":"2020-02-19T21:41:01+08:00","vendor":"diymore","type":"Motor Speed Controller","tags":[],"price":1599,"price_min":1599,"price_max":1899,"available":true,"price_varies":true,"compare_at_price":null,"compare_at_price_min":0,"compare_at_price_max":0,"compare_at_price_varies":false,"variants":[{"id":31776718946375,"title":"5A-TB6600","option1":"5A-TB6600","option2":null,"option3":null,"sku":"010700","requires_shipping":true,"taxable":true,"featured_image":{"id":14509377224775,"product_id":4490370023495,"position":2,"created_at":"2020-05-06T01:56:08+08:00","updated_at":"2020-05-06T01:56:13+08:00","alt":"4A 5A Tb6600 Single Axis Stepper Motor Driver Controller Board Cnc Engraving Machine 1 Stepping","width":1000,"height":1000,"src":"\/\/www.diymore.cc\/cdn\/shop\/products\/He236654ff01e4461b3907273c5ea2dd0z_683.jpg?v=1588701373","variant_ids":[31776718946375]},"available":true,"name":"4A 5A TB6600 Single Axis Stepper Motor Driver Controller Board CNC Engraving Machine 1 Axis Stepping Motor Driver Module - 5A-TB6600","public_title":"5A-TB6600","options":["5A-TB6600"],"price":1899,"weight":0,"compare_at_price":null,"inventory_management":null,"barcode":"","featured_media":{"alt":"4A 5A Tb6600 Single Axis Stepper Motor Driver Controller Board Cnc Engraving Machine 1 Stepping","id":6682564100167,"position":2,"preview_image":{"aspect_ratio":1.0,"height":1000,"width":1000,"src":"\/\/www.diymore.cc\/cdn\/shop\/products\/He236654ff01e4461b3907273c5ea2dd0z_683.jpg?v=1588701373"}},"requires_selling_plan":false,"selling_plan_allocations":[]},{"id":31776718979143,"title":"4A-TB6600","option1":"4A-TB6600","option2":null,"option3":null,"sku":"010740","requires_shipping":true,"taxable":true,"featured_image":{"id":14509377650759,"product_id":4490370023495,"position":3,"created_at":"2020-05-06T01:56:12+08:00","updated_at":"2020-05-06T01:56:13+08:00","alt":"4A 5A Tb6600 Single Axis Stepper Motor Driver Controller Board Cnc Engraving Machine 1 Stepping","width":1000,"height":1000,"src":"\/\/www.diymore.cc\/cdn\/shop\/products\/Ha8b2526e84444ee9a78aea20742ee77e8_352.jpg?v=1588701373","variant_ids":[31776718979143]},"available":true,"name":"4A 5A TB6600 Single Axis Stepper Motor Driver Controller Board CNC Engraving Machine 1 Axis Stepping Motor Driver Module - 4A-TB6600","public_title":"4A-TB6600","options":["4A-TB6600"],"price":1599,"weight":0,"compare_at_price":null,"inventory_management":null,"barcode":"","featured_media":{"alt":"4A 5A Tb6600 Single Axis Stepper Motor Driver Controller Board Cnc Engraving Machine 1 Stepping","id":6682564427847,"position":3,"preview_image":{"aspect_ratio":1.0,"height":1000,"width":1000,"src":"\/\/www.diymore.cc\/cdn\/shop\/products\/Ha8b2526e84444ee9a78aea20742ee77e8_352.jpg?v=1588701373"}},"requires_selling_plan":false,"selling_plan_allocations":[]}],"images":["\/\/www.diymore.cc\/cdn\/shop\/products\/4A_5A_TB6600_Single_Axis_Stepper_Motor_Driver_Controller_Board_CNC_Engraving_Machine_1_Axis_Stepping_565.jpg?v=1588701373","\/\/www.diymore.cc\/cdn\/shop\/products\/He236654ff01e4461b3907273c5ea2dd0z_683.jpg?v=1588701373","\/\/www.diymore.cc\/cdn\/shop\/products\/Ha8b2526e84444ee9a78aea20742ee77e8_352.jpg?v=1588701373"],"featured_image":"\/\/www.diymore.cc\/cdn\/shop\/products\/4A_5A_TB6600_Single_Axis_Stepper_Motor_Driver_Controller_Board_CNC_Engraving_Machine_1_Axis_Stepping_565.jpg?v=1588701373","options":["Style"],"media":[{"alt":"4A 5A Tb6600 Single Axis Stepper Motor Driver Controller Board Cnc Engraving Machine 1 Stepping","id":6682563870791,"position":1,"preview_image":{"aspect_ratio":1.0,"height":1000,"width":1000,"src":"\/\/www.diymore.cc\/cdn\/shop\/products\/4A_5A_TB6600_Single_Axis_Stepper_Motor_Driver_Controller_Board_CNC_Engraving_Machine_1_Axis_Stepping_565.jpg?v=1588701373"},"aspect_ratio":1.0,"height":1000,"media_type":"image","src":"\/\/www.diymore.cc\/cdn\/shop\/products\/4A_5A_TB6600_Single_Axis_Stepper_Motor_Driver_Controller_Board_CNC_Engraving_Machine_1_Axis_Stepping_565.jpg?v=1588701373","width":1000},{"alt":"4A 5A Tb6600 Single Axis Stepper Motor Driver Controller Board Cnc Engraving Machine 1 Stepping","id":6682564100167,"position":2,"preview_image":{"aspect_ratio":1.0,"height":1000,"width":1000,"src":"\/\/www.diymore.cc\/cdn\/shop\/products\/He236654ff01e4461b3907273c5ea2dd0z_683.jpg?v=1588701373"},"aspect_ratio":1.0,"height":1000,"media_type":"image","src":"\/\/www.diymore.cc\/cdn\/shop\/products\/He236654ff01e4461b3907273c5ea2dd0z_683.jpg?v=1588701373","width":1000},{"alt":"4A 5A Tb6600 Single Axis Stepper Motor Driver Controller Board Cnc Engraving Machine 1 Stepping","id":6682564427847,"position":3,"preview_image":{"aspect_ratio":1.0,"height":1000,"width":1000,"src":"\/\/www.diymore.cc\/cdn\/shop\/products\/Ha8b2526e84444ee9a78aea20742ee77e8_352.jpg?v=1588701373"},"aspect_ratio":1.0,"height":1000,"media_type":"image","src":"\/\/www.diymore.cc\/cdn\/shop\/products\/Ha8b2526e84444ee9a78aea20742ee77e8_352.jpg?v=1588701373","width":1000}],"requires_selling_plan":false,"selling_plan_groups":[],"content":"\u003cdiv class=\"detailmodule_text-image\"\u003e\n\u003cp class=\"detail-desc-decorate-title\" data-spm-anchor-id=\"a2g0o.detail.1000023.i0.18421cf5ZdYzqP\"\u003e\u003cstrong\u003e4A-TB6600\u003c\/strong\u003e\u003cbr\u003e\u003cbr\u003eSpecifications:\u003cbr\u003eSupply Voltage: 9~42VDC\u003cbr\u003eMax Drive Current: 4A\u003cbr\u003eChopping Frequency: 20KHZ\u003cbr\u003e \u003cbr\u003eFeatures:\u003cbr\u003eBipolar constant current chopper\u003cbr\u003eHigh-speed optocoupler signal isolation input\u003cbr\u003eElectrical input signal is TTL compatible\u003cbr\u003eStationary current is automatically reduced by half\u003c\/p\u003e\n\u003cimg src=\"https:\/\/ae01.alicdn.com\/kf\/Ha8b2526e84444ee9a78aea20742ee77e8.jpg\" class=\"detail-desc-decorate-image\"\u003e\u003cimg src=\"https:\/\/ae01.alicdn.com\/kf\/H839a8652f0184ef1b95d3dcffecbbc93W.jpg\" class=\"detail-desc-decorate-image\"\u003e\u003cimg src=\"https:\/\/ae01.alicdn.com\/kf\/Hbc427740876349ef8df4d15bec752e8dA.jpg\" class=\"detail-desc-decorate-image\"\u003e\n\u003c\/div\u003e\n\u003cdiv class=\"detailmodule_text-image\"\u003e\n\u003cp class=\"detail-desc-decorate-title\"\u003e\u003cstrong\u003e5A-TB6600\u003c\/strong\u003e\u003cbr\u003e\u003cbr\u003eHY-DIV268N-5A subdivision-type two-phase hybrid stepping motor drive using DC 12 ~ 48V power supply, suitable for drive\u003cbr\u003eTwo-phase hybrid stepping motor dynamic voltage 12 to 48V, the current is less than 5A outer diameter of 35 to 86 mm. This drive using the drive's current loop subdivision control, the motor torque ripple is very small, low-speed running is very smooth, almost no vibration and noise. High-speed torque is much higher than other two-phase drive, high positioning accuracy. Widely used in the engraving machine, CNC machine tools, packaging machinery and other high resolution requirements on the device.\u003cbr\u003e\u003cbr\u003eThe main features\u003cbr\u003e- average current control, two-phase sinusoidal current drive output\u003cbr\u003e- DC 12 ~ 48V power supply, the internal integration of 12V and 5V regulator\u003cbr\u003e- optically isolated signal input \/ output\u003cbr\u003e- overvoltage, undervoltage, overcurrent, and white short-circuit protection\u003cbr\u003e\u003cbr\u003e- Input voltage DC 12 ~ 48V input\u003cbr\u003e- The input current of 1 to 5 amps, select the drive a stepper motor.\u003cbr\u003e- Output current of 0.2A ~ 5A\u003cbr\u003e- Temperature Operating Temperature -10 to 45 ℃; Storage temperature -40 ℃ to 70 ℃\u003cbr\u003e- Humidity not condensing, not drops\u003cbr\u003e- Gas prohibit combustible gas and conductive dust\u003cbr\u003e- Weight 200 grams\u003cbr\u003e\u003cbr\u003eControl signal interface\u003cbr\u003e- Figure 1 is a wiring schematic of the drive\u003cbr\u003e- 1, the definition of control signals\u003cbr\u003ePUL +: step pulse signal is input side or the positive pulse signal input positive terminal\u003cbr\u003ePUL-: the negative input of the negative input pulse signal or a positive pulse signal\u003cbr\u003eDIR +: stepping direction signal input to the positive terminal or negative pulse signal input to the positive terminal\u003cbr\u003eDIR -: stepping direction signal input of the negative side or reverse step pulse signal input negative terminal\u003cbr\u003eEN +: offline can reset signal input side is\u003cbr\u003eEN-: offline can reset signal input negative terminal\u003cbr\u003eOffline enable signal is active, reset drive failure to prohibit any pulse, the output of the drive\u003cbr\u003ePower component is turned off, the motor holding torque.\u003cbr\u003e- Control signal connections\u003cbr\u003e- PC control signal can be high, also can be low effective. When active high, the control signal\u003cbr\u003e- The negative side together as a signal to active low, positive side of all control signals together as a signal common.\u003cbr\u003e- For example, open-collector and PNP output interface circuit diagram is as follows:\u003cbr\u003eFigure 2. Input interface circuit (common cathode connection)\u003cbr\u003e- Note: the VCC is 5V, R short;\u003cbr\u003e- VCC value of 12V, R 1K, more than 1\/8W resistor;\u003cbr\u003e- VCC value of 24V, R 2K, more than 1\/8W resistor;\u003cbr\u003e\u003cbr\u003eFunction selection (DIP switch on the drive panel)\u003cbr\u003e- Set the motor per revolution steps\u003cbr\u003eThe drive to set the number of steps per motor revolution is 200 (whole step), 400 (2 segments), 1600 (8 segments), 3200 steps (16 segments).\u003cbr\u003eThe user can drive the front panel DIP switch SW3 is SW4 bit of the drive to set the number of steps (such as Table 1):\u003cbr\u003eTable 1\u003cbr\u003e- Set the output phase current\u003cbr\u003e- To drive torque stepper motor, the user can drive panel DIP switch\u003cbr\u003e- SW1, SW2 is to set the drive output phase current (RMS) unit amperes, the switch position\u003cbr\u003e- Corresponding to the output current, output current value corresponding different types of drive. Concrete are shown in Table 2.\u003cbr\u003e- Output Current (A\u003cbr\u003eTable 2\u003cbr\u003eCurrent setting\u003cbr\u003e\u003cbr\u003e- the semi-flow functionality\u003cbr\u003e- The semi-flow function is a step pulse 200ms, the driver output current is automatically reduced to the rated output current50%, used to prevent motor heating.\u003cbr\u003eFourth, the power interface\u003cbr\u003e- 1, DC +, DC-: to connect the drive power\u003cbr\u003e- DC +: DC power level, power supply voltage DC 12 to 48V. The maximum current is 5A. The\u003cbr\u003eDC-: DC power supply negative level.\u003cbr\u003e2, A + A-B + B-: to connect the two-phase hybrid stepping motor\u003cbr\u003eDrive and two-phase hybrid stepper motor's connection with the four-wire system, the motor windings in parallel and series connection, and connection method, high-speed performance, but the drive current is large (for motor winding current of 1.73 times), Connected in series when the drive current is equal to the motor winding current.\u003cbr\u003eFive, the installation\u003cbr\u003e- Around to have 20mm of space, can not be placed next to the other heating equipment, to avoid dust, oil mist,\u003cbr\u003eCorrosive gases, high humidity is too big and strong vibration. +\u003cbr\u003eFigure 3.\u003cbr\u003eSix fault diagnosis\u003cbr\u003e1, the status light indicates\u003cbr\u003eRUN: green light in the normal work.\u003cbr\u003eERR: red light, power, light, power indicator\u003cbr\u003eSize: 10.5x8.5x3.3cm(approx)\u003c\/p\u003e\n\u003cimg src=\"https:\/\/ae01.alicdn.com\/kf\/He236654ff01e4461b3907273c5ea2dd0z.jpg\" class=\"detail-desc-decorate-image\"\u003e\u003cimg src=\"https:\/\/ae01.alicdn.com\/kf\/H77553a99bd4e46368cda2f21564c0af9p.jpg\" class=\"detail-desc-decorate-image\"\u003e\u003cimg src=\"https:\/\/ae01.alicdn.com\/kf\/Hc397f6a15fe8431bbcb8fe86468830fbk.jpg\" class=\"detail-desc-decorate-image\"\u003e\u003cimg src=\"https:\/\/ae01.alicdn.com\/kf\/Hc150b70a72af438d9ca4dea9bb464a43A.jpg\" class=\"detail-desc-decorate-image\"\u003e\u003cimg src=\"https:\/\/ae01.alicdn.com\/kf\/H2d60bfbea92d45ff9898a39239cf0c88d.jpg\" class=\"detail-desc-decorate-image\"\u003e\n\u003c\/div\u003e"}